Friction stir welding (FSW) is a solid-state welding process used to join materials such as aluminum and copper. It relies on friction and pressure, without melting the metal.
Appreciated in demanding sectors, this method impresses with its precision and durability. It delivers reliable, strong and flawless welds. FSW can be used to produce complex assemblies of excellent quality.
Thanks to the absence of fusion, friction welding limits distortion and improves weld repeatability. It can be easily integrated into automated lines. Friction welding is just as well-suited to thin parts as it is to large structures.
But what are the different applications of friction stir welding? In this article, TRA-C industrie, specialist in industrial welding and FSW, gives you a complete overview of the different industrial sectors concerned by friction stir welding…
Understanding the friction stir welding process
Friction stir welding is a welding process that does not involve the melting of metals. A rotating tool generates heat by friction, softening the material. The tool then advances to mix the weld line and create a homogeneous weld.
This technique is particularly suitable for light alloys, such as aluminum, copper or magnesium. It is also effective on certain steels and composites, with specific tools. FSW enables solid assemblies without the addition of filler metal.
Advantages include excellent joint quality, with no porosity or cracks. The absence of electric arc or gas makes the process safer and more environmentally friendly. Furthermore, welding requires little or no surface preparation!
Friction welding also helps to limit part deformation, thanks to a lower welding temperature than conventional processes. This thermal control preserves the mechanical properties of materials.
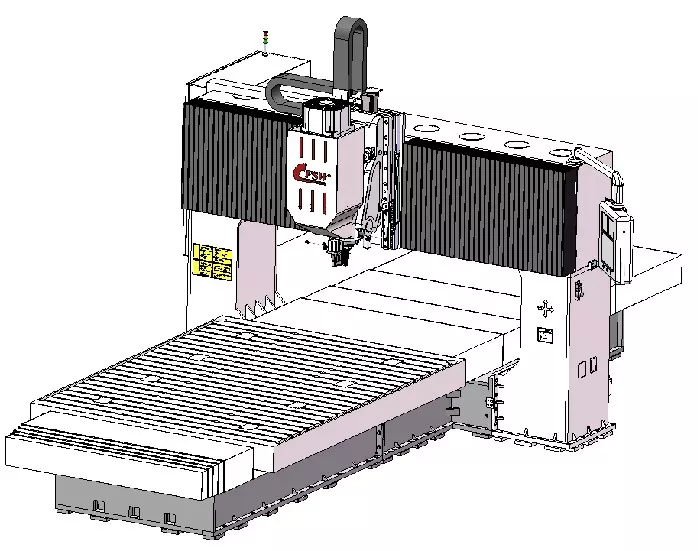

Application of friction stir welding in the automotive industry
In the automotive industry, manufacturers make extensive use of friction stir welding to assemble aluminum parts. This lightweight material helps to reduce vehicle weight and therefore, energy consumption.
The process is ideal for the assembly of body panels, battery trays, heat exchangers, structural components and more. It provides excellent precision, even on thin or complex parts, reducing the costs associated with rework or welding defects.
Thanks to automation, FSW can be easily integrated into automotive production lines. It offers high reproducibility and reduced cycle times. Its ability to work without adding filler metal also simplifies industrial logistics.
Last but not least, this method meets growing safety and quality requirements. It helps to improve vehicle performance while complying with environmental standards. It is thus a key asset for tomorrow’s mobility…
The role of FSW in the aerospace industry
Friction stir welding is the welding solution of choice in the aerospace industry. It enables lightweight materials to be joined with consistent quality. The process ensures highly resistant joints, essential in extreme conditions.
Fuselages, fuel tanks and structural panels are often FSW welded. The absence of fusion prevents internal defects such as porosity or cracks. It therefore guarantees high reliability for critical aircraft parts!
Thanks to its precision, FSW limits thermal deformation and rework. It also reduces the overall weight of structures, optimizing flight performance. This weight saving is essential for autonomy and fuel consumption.
Used in both civil and space aeronautics, the process is particularly robust. It meets the stringent regulatory requirements of this sector. It thus contributes to safety, efficiency and innovation in the aerospace industry.

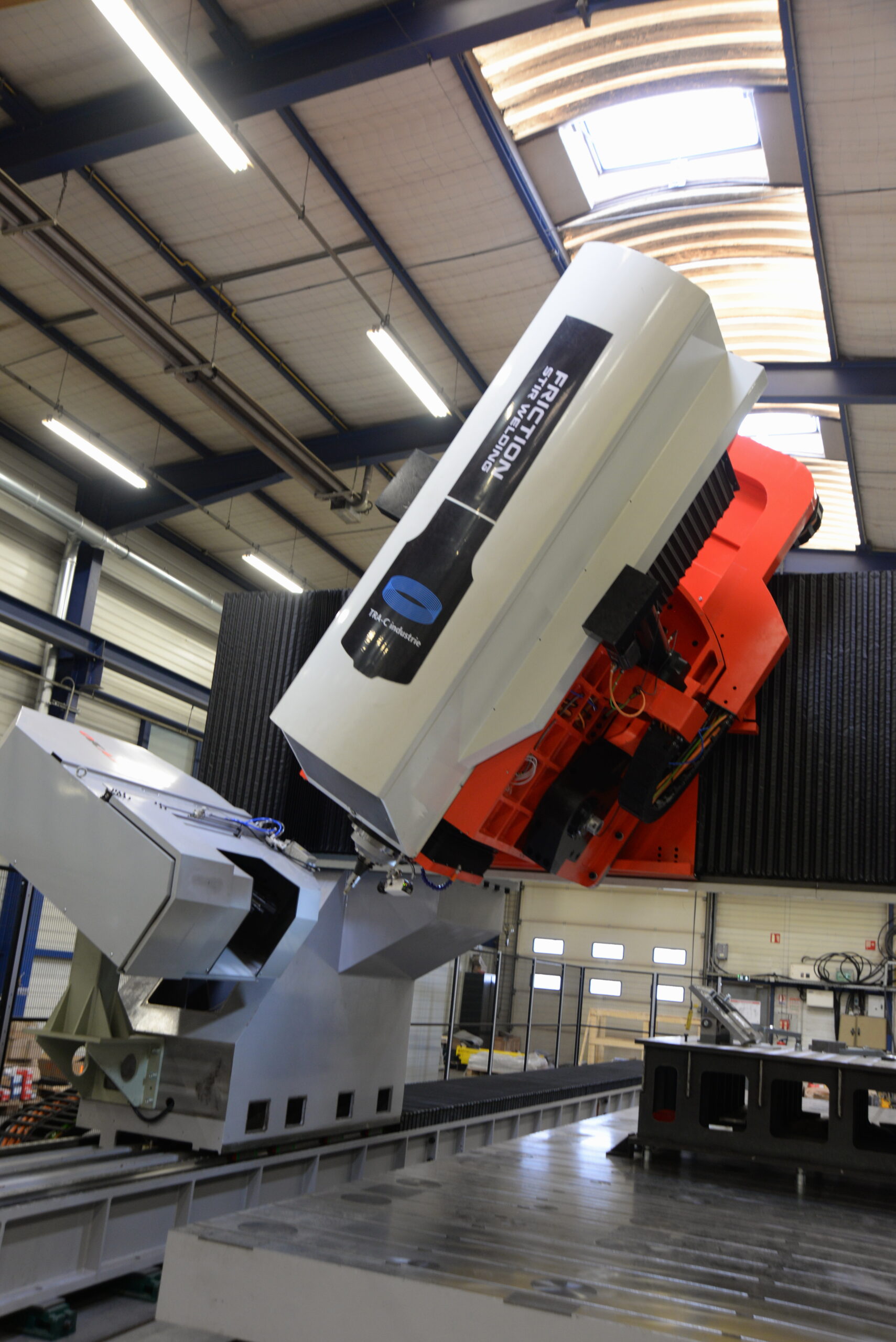
Using FSW in the rail sector
The rail industry uses friction stir welding to design structures that are both light and strong. It enables large aluminum panels to be assembled with excellent mechanical continuity. The result is greater safety and longer vehicle life.
FSW is ideal for the production of floors, roofs, sidewalls and wagon bodies. It guarantees long, regular welds with no internal defects. This process improves resistance to vibration and shock during operation.
The absence of melting also reduces part deformation and minimizes rework. The process, which can be easily automated, is ideally suited to mass production. It ensures homogeneous assemblies on large parts…
This welding method also helps to reduce the weight of trains, making them more energy-efficient. Here too, it meets the challenges of efficiency, safety and sustainability in modern rail transport.
Friction stir welding for the shipbuilding industry
In the marine industry, friction stir welding is used to join aluminum structures to hulls, decks and bulkheads. The process produces watertight, resistant welds, essential in marine environments.
FSW provides excellent mechanical resistance, even in salty or damp environments. It limits the risk of corrosion and extends the service life of assemblies. This makes it an ideal solution for shipbuilding, yachting and military vessels!
This process is also appreciated for its ability to weld long lengths without interruption. It reduces defects and avoids distortion, thus reducing the need for rectification. This saves production time and quality.
Finally, this technique meets the stringent technical requirements of the naval sector. It makes it possible to combine lightness, strength and durability of structures while complying with maritime safety standards. It is becoming standard in modern shipbuilding.

Towards new friction stir welding applications
Friction stir welding is finally opening up to innovative fields, driven by technological developments and industrial needs. Sectors such as electronics, batteries and renewable energies are actively exploring this process.
In the manufacture of batteries for electric vehicles, FSW ensures conductive welds without excessive heating. It enables aluminum cases to be assembled without damaging sensitive components. It’s a real asset for e-mobility.
The renewable energies sector, notably solar and wind power, also uses FSW for its metal components. It guarantees high durability and excellent corrosion resistance. This process optimizes the reliability of installations over time.
Finally, friction stir welding is increasingly associated with additive manufacturing and 3D metal printing. It is used to consolidate complex or hybrid parts. This synergy opens the way to innovative applications in the industry of the future…
Call on a specialist for your friction stir welding applications
Friction stir welding has many applications in the automotive, aerospace, rail and naval industries. This process ensures solid, precise and durable welds. It meets the growing demands for industrial performance and innovation.
But to guarantee reliable results, it makes sense to call in an FSW specialist. An expert will know how to adapt the process to the alloys, shapes and constraints of each sector. He will therefore optimize quality, safety and productivity!
European leader in friction stir welding, TRA-C industrie supports its customers in complex technical projects. Drawing on our know-how and solid experience, we are involved from the R&D phase through to series production and welding machine integration.
Groups such as Arquus, Thalès and Stellantis rely on us for their FSW applications. This recognition underlines our company’s expertise in a wide range of industrial fields. TRA-C industrie is now a recognized player in the welding sector.
