How does friction stir welding meet the challenges of e-mobility?
In a world of constant change and environmental challenges, e-mobility is growing rapidly, shaping the future of the automotive industry.
Faced with increasingly stringent regulations and growing demand for environmentally-friendly vehicles, the e-mobility sector must constantly innovate to meet consumer expectations and today’s challenges!
At the heart of this new industrial revolution, friction stir welding (FSW) is becoming an essential technology.
But what exactly is e-mobility? What are the needs of this sector? And what are the advantages of FSW in this field? In this article, TRA-C industrie tells you more about the applications of FSW for the sustainable automotive industry...

What is the e-mobility sector?
E-mobility, or electric mobility, refers to the use of “clean” means of locomotion. These are electric or hybrid vehicles (cars, buses, scooters, bicycles) as well as the infrastructure needed to operate them.
The main goal of this sector is to reduce dependence on fossil fuels and promote more sustainable, environmentally-friendly options of transport...
E-mobility has completely rethought the propulsion system of modern vehicles. The need to integrate new components, such as rechargeable batteries and electric motors, has led to a drastic change in vehicle design.
To keep pace with these developments, car manufacturers have had to adapt their production techniques in order to offer vehicles that are aesthetically pleasing, clean and, above all, reliable!
Needs of the e-mobility industry
In view of the current environmental challenges, today’s needs in the e-mobility field are numerous. These include:
- Integration of new components: such as high-voltage batteries, electric motors and recharging connectors. These components require specific integration, which imposes particular requirements in terms of design;
- A revised design: in order to optimise the performance of electric and hybrid vehicles, carmakers need to rethink the arrangement of components, aerodynamics and thermal management;
- The use of new materials: batteries in particular are made of aluminium, copper and graphite. These materials have unique characteristics and therefore require specific manufacturing and assembly techniques;
- Reduction of materials in use: to improve the fuel efficiency of vehicles, we need to limit the weight of components while maintaining safety and performance standards;
- Strict environmental standards: Environmental regulations are increasingly demanding in terms of emissions and energy efficiency. To meet them, the industry must constantly innovate;
- A need for qualified staff: researchers, engineers, electrical technicians, roboticists, etc. The design, manufacture and assembly of more environmentally-friendly components require a highly skilled workforce.
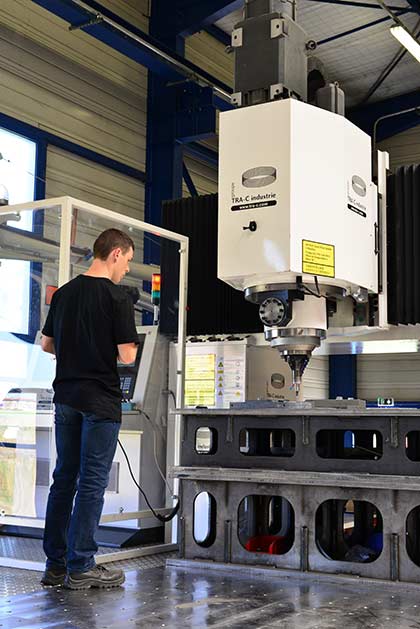
The benefits of friction stir welding in the e-mobility field
To adapt to the growing needs of the e-mobility sector, the manufacture of electric and hybrid vehicles requires cutting-edge technologies. Friction stir welding appears to be a suitable solution.
FSW is now mainly used in “sensitive” sectors such as rail, aeronautics, defence and space. The process produces the high-quality solid-state welds required in these sectors.
During its welding process, the FSW maintains constant pressure on the parts with a rotating tool. The part to be welded is then heated, making it malleable. Its properties are also preserved, since no material is added!
Vehicles powered by alternative energy sources require specific materials that are used in the construction of batteries and other key e-mobility components (aluminium, copper).
FSW differs from other welding techniques because it can be used to assemble these materials and light alloys. The advantages of this process include:
- Virtually no deformation
- Lack of porosity
- Improved mechanical properties
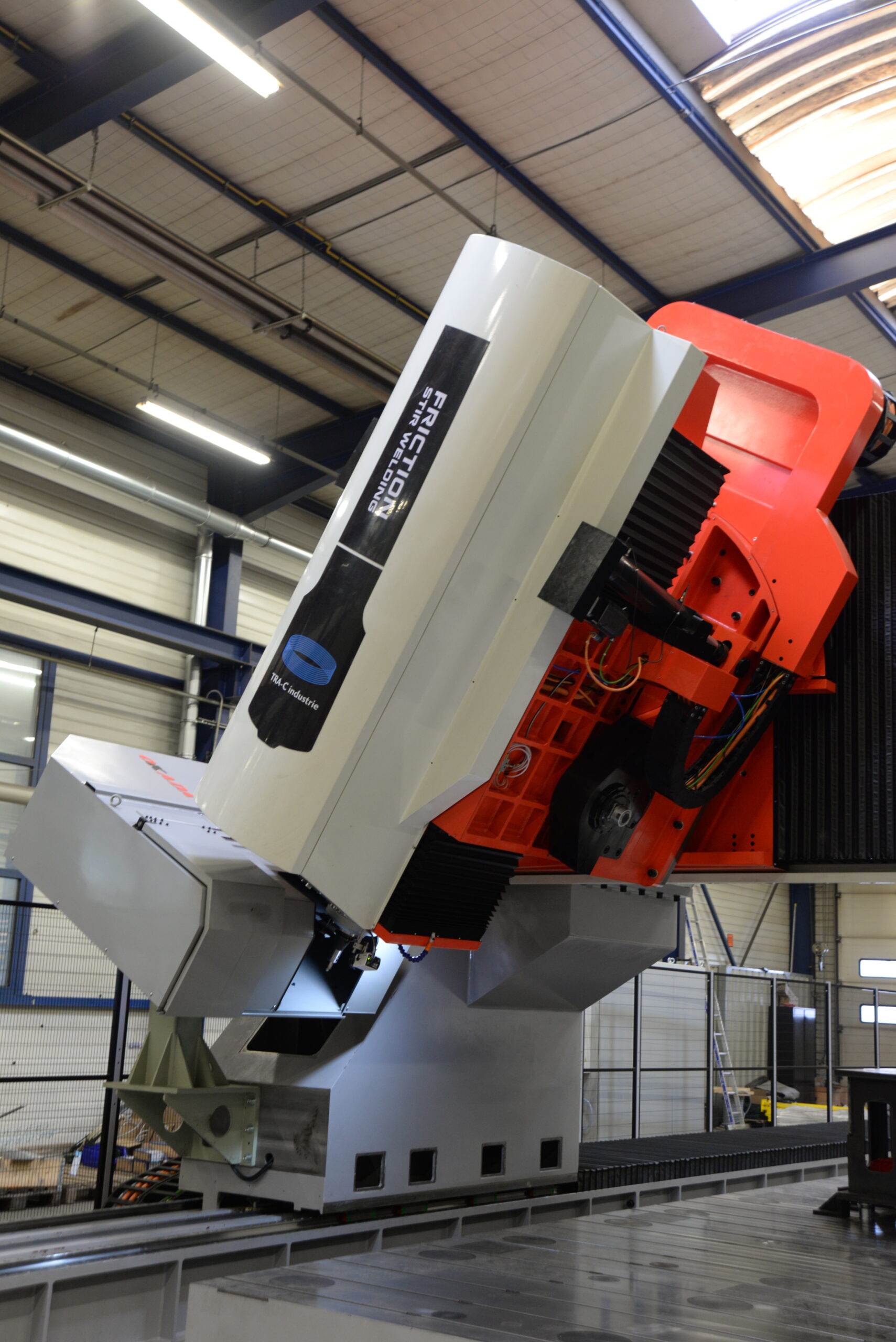
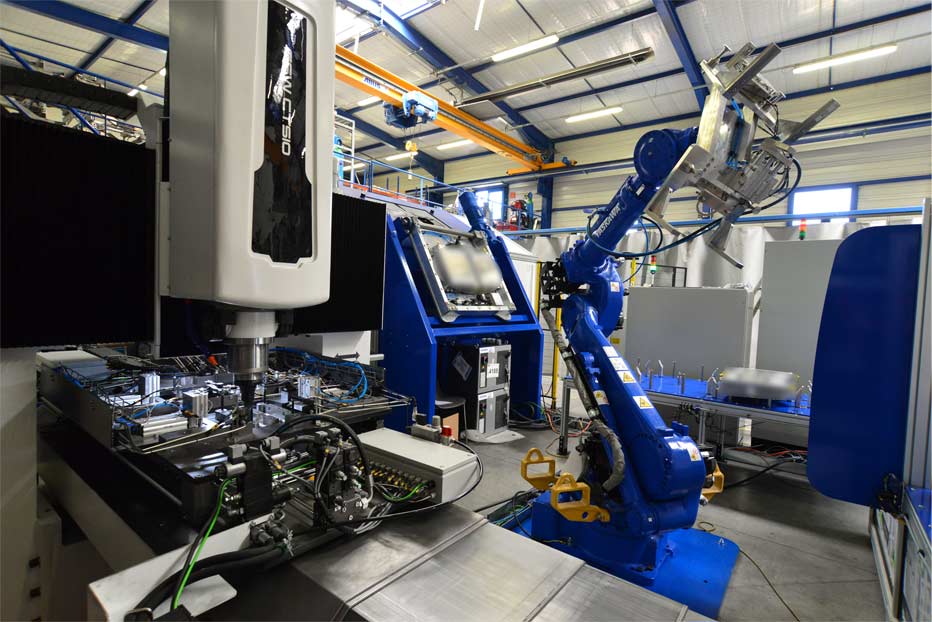
Another major advantage of this welding technique: parts are lighter. FSW requires no filler metal, offering weight savings of up to 30%. This is particularly relevant when assembling aluminium components, as this alloy is particularly light in weight…
Apart from the technical aspects, FSW is a clean, environmentally-friendly welding technology that is ideally suited to the e-mobility sector. Unlike other welding techniques, its process enables:
- Energy savings of up to 20%, as no external heat supply is required
- No UV radiation, toxic emissions or smoke
- No material spillage, offering greater safety for employees
- A limited quantity of waste in the absence of input metal
Use of FSW in the e-mobility sector
Stiffened panels
Stiffened panels are components used for vehicle floors and the structure of battery boxes. Because these parts are subject to high mechanical stress, their welding must be strong and durable.
The FSW process makes it possible to assemble large panels. Aluminium profiles, which must be less than 400 mm long, can now be butt-welded to overcome this limitation.
Friction stir welding also makes the panels lighter, as there is no additional material for welding. Electric and hybrid vehicles are themselves lighter, which reduces their energy consumption.
The defence sector, for example, chooses this process to assemble their vehicles. Renowned manufacturers such as Nexter use this welding technique to increase the reliability of their assemblies and the durability of their products.
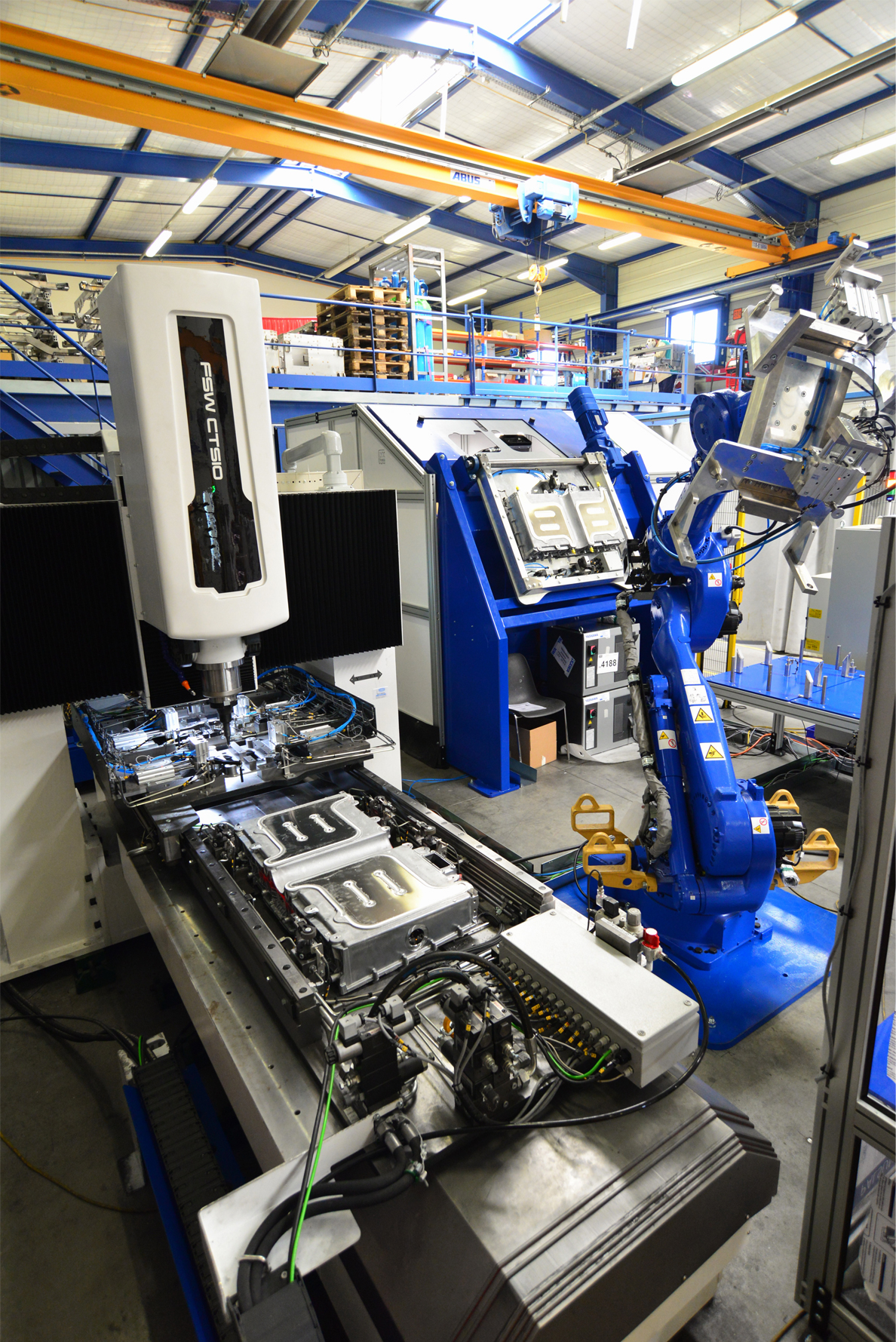
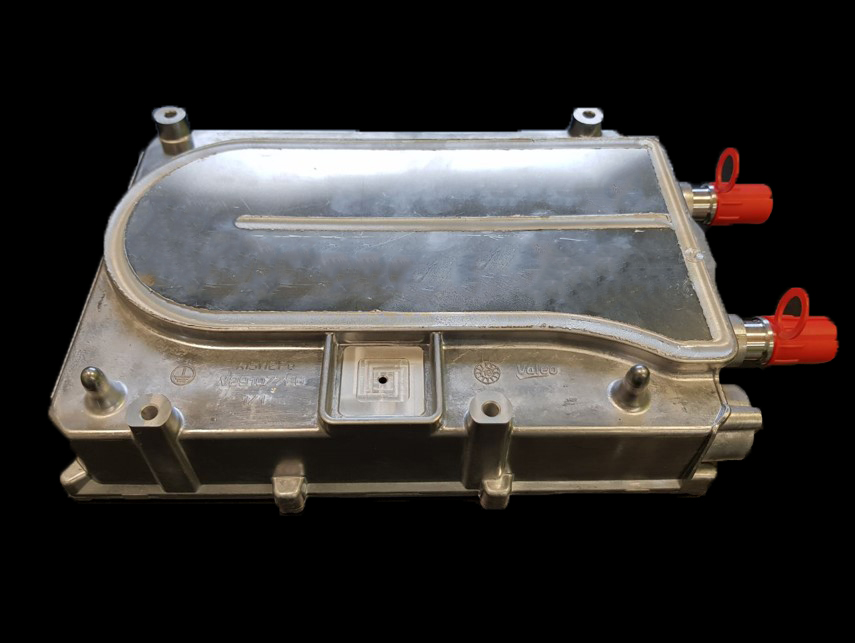
Heat exchangers
Manufactured from profiled aluminium parts, the heat exchanger plays a major role in cooling the electronic components of hybrid and electric vehicles.
It must be assembled to guarantee a perfect seal and high mechanical strength. Friction stir welding passes remarkably the watertightness tests…
Because of the welds’ high quality, FSW reduces the need to screw components together. This process therefore allows the manufacturer to save time during the production process.
Battery containers
Battery boxes, which are essential for housing and protecting batteries from electric vehicles, must have good electrical conductivity.
The FSW process enables this very property to be maintained when the boxes are assembled. This is possible because of the excellent quality of the welds and the minimal melting of the parts.
Finally, friction stir welding is a cold-welding process. It therefore does not damage the electrical components during the process…
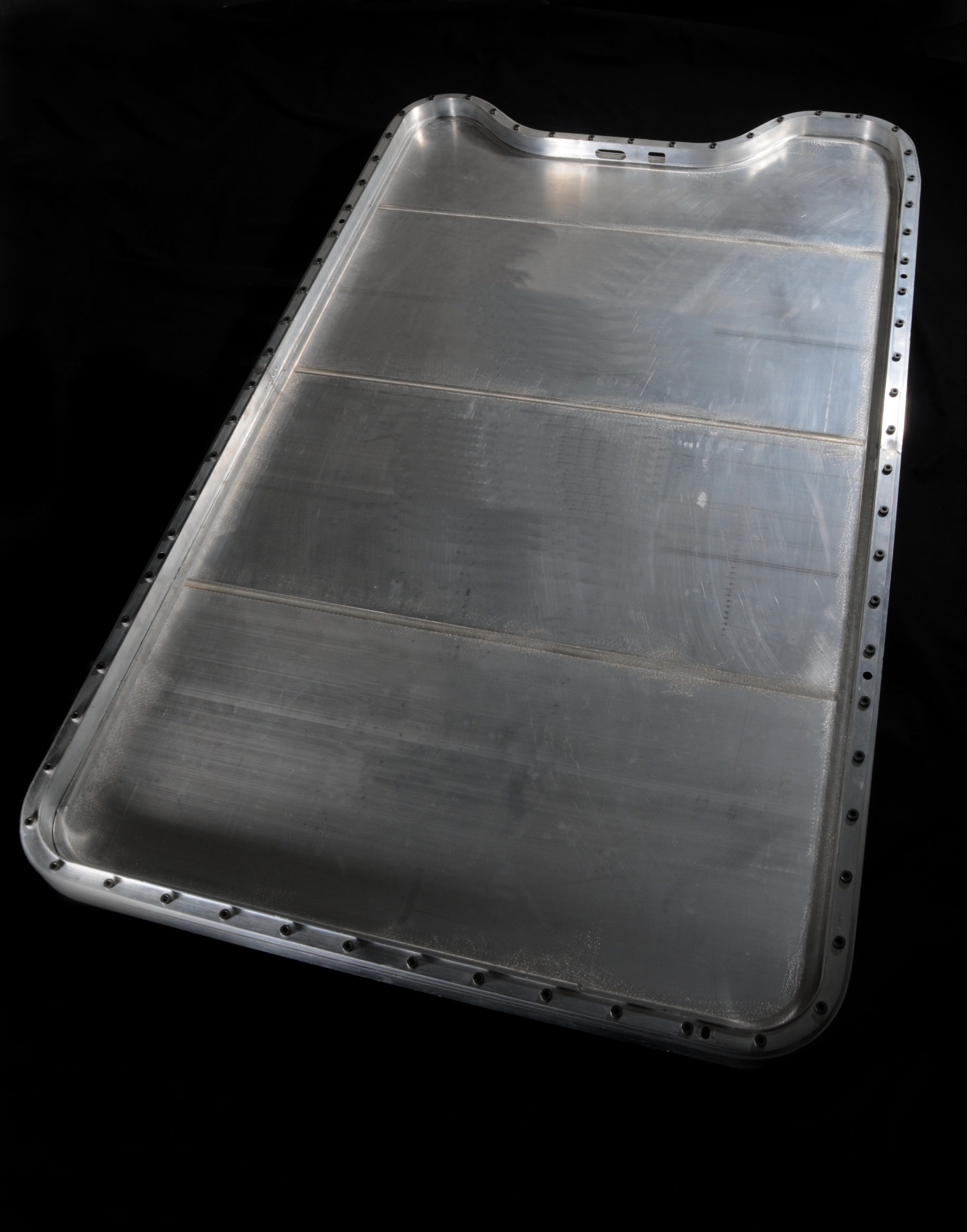
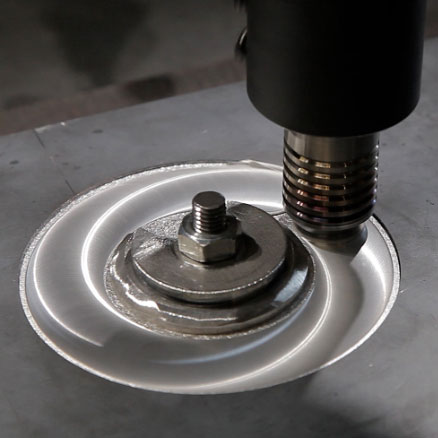
Engine blocks
Friction stir welding is also used in the manufacture of engine blocks for electric vehicles. Like the battery cases, they are made of aluminium and steel. Today, only the FSW process can efficiently assemble these alloys.
Another interesting fact: FSW can be used for welding in all configurations. It is therefore particularly suitable to manufacture complex components such as engine blocks. They often have specific shapes to accommodate the various components.
Chargers
The manufacture of chargers is strategic for car manufacturers. Thanks to the friction stir welding process, it is possible to precisely control every parameter during the welding process.
Operators can then optimise and meticulously check the quality of the assemblies, which is essential in the manufacture of reliable and efficient chargers.
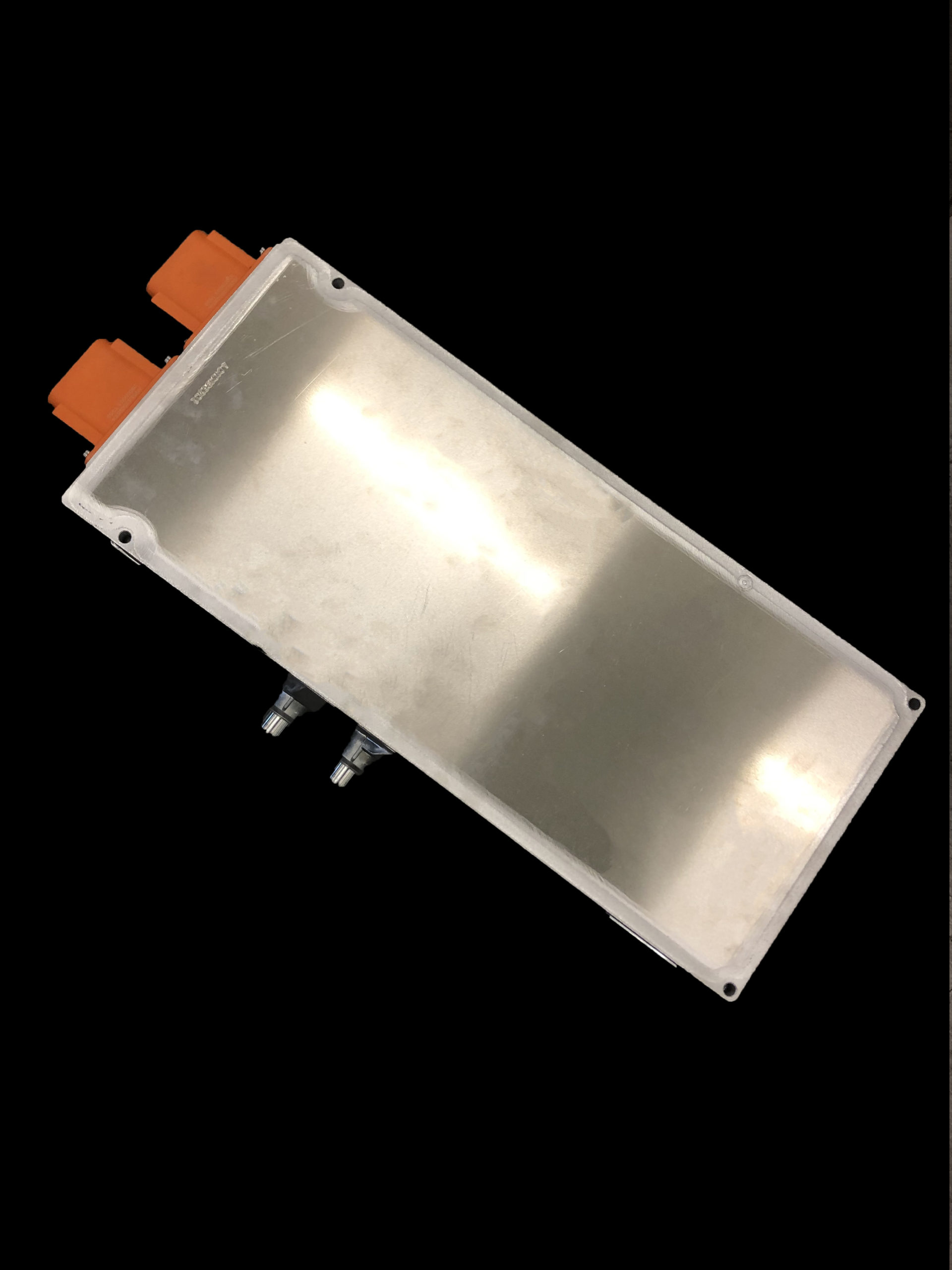
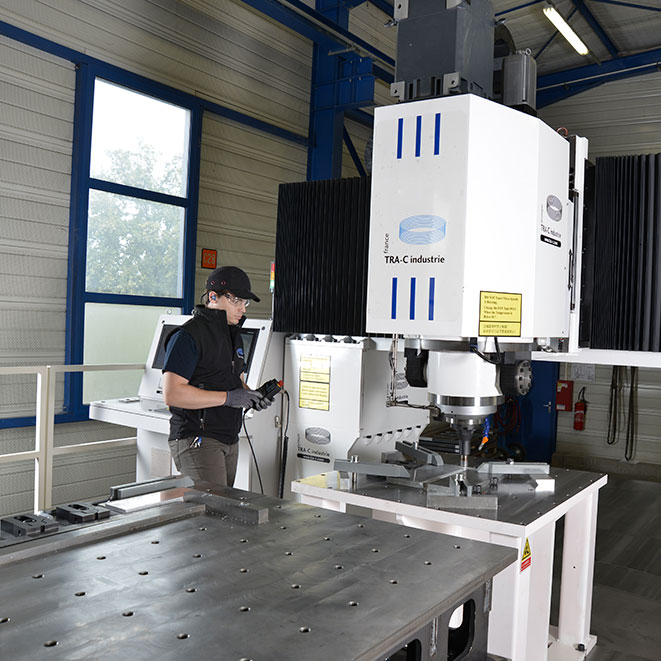
How does FSW ensure the sustainability of production lines?
Friction stir welding now makes it possible to ensure the long-term viability of production lines in the e-mobility sector in particular, thanks to:
- Fast, cost-effective production by optimising assembly operations
- Creation of high-quality, durable welds, increasing the reliability of assemblies
- Integration of human-machine interfaces (HMI) for real-time production monitoring
By investing in FSW, companies have access to a technology that is safe, efficient and adaptable to the new demands of the automotive sector. They can also anticipate periods of economic crisis and adjust their production lines accordingly.
TRA-C industrie, expert in friction stir welding for e-mobility
Thanks to its high-quality welds, flexibility with regard to new materials and optimisation of cost-effectiveness, FSW id now a solution to competitiveness, sustainability and regulatory compliance in the automotive industry.
Friction stir welding is an environmentally-friendly welding technique that is essential for automotive manufacturers, because it reduces waste, makes components lighter and emits no toxic vapours, radiation or particles.
With 9 production sites in France and a workshop in Canada, TRA-C industrie is the European leader in friction stir welding for the automotive industry. We are also experts in the design and manufacture of fully robotised assembly cells.
Today, the company can count on its strong expertise to support e-mobility stakeholders in integrating FSW into their electric and hybrid vehicle manufacturing processes.
TRA-C industrie can manufacture your sub-assemblies in small, medium and large series. Our experts are at your side at every stage of your project, from design to assembly, including the manufacture of your engine blocks, exchangers, chargers, etc.
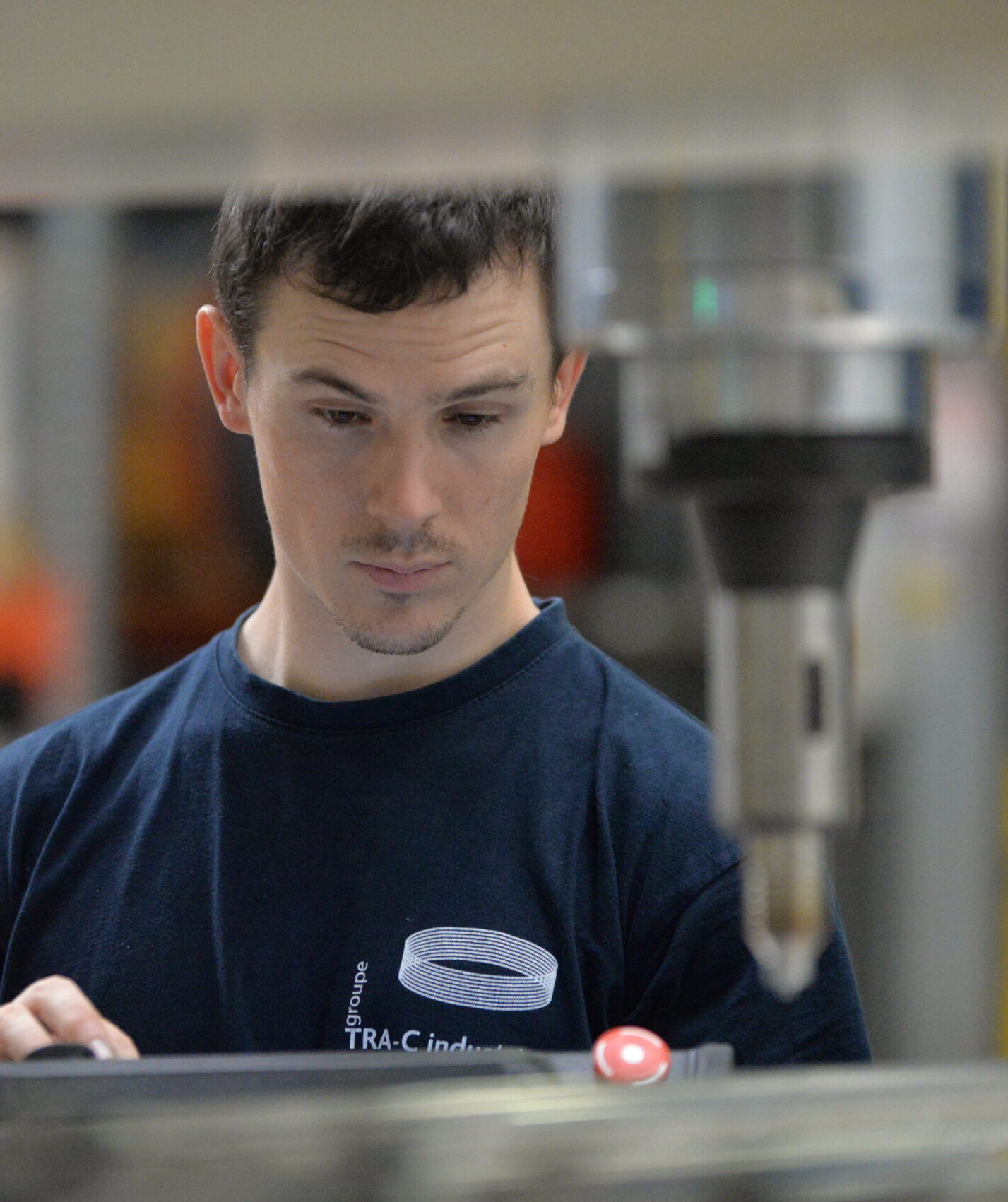
Are you an e-mobility professional? Would you like to find out more about the FSW principle and its benefits for your company? TRA-C industrie is here to help :