EN 15085 standard and welding in the railway industry
The EN 15085 standard guarantees the safe welding of railway vehicles and components. It is now the reference regulation in Europe for the railway sector.
With a total length of 27,057 km of railway lines in 2021, more than 122 million high-speed train passengers in 2023, and billions of tons of goods carried, the railway industry is growing fast and needs to be efficient and safe!
To meet this requirement, professionals in the railway sector must be cautious about the quality of their components and their manufacturing processes. The safety of users is at stake. ISO 15085 was purposefully designed to provide a framework for manufacturers.
But what is EN 15085 standard? What are its aims? And which welding techniques can be certified? In this article, TRA-C industrie tells you all about the importance of these regulations for the railway sector…

What is EN 15085 standard?
Also known as the “European Railway Welding Standard“, EN 15085 was first introduced in 2005. It was developed by the European Committee for Standardisation (CEN) to provide a framework for welding operations in the railway industry.
This regulation is actually a set of standards. They are all linked to the EN 3834 standard entitled “Quality requirements for fusion welding of metallic materials”. The aim is to create a global framework for companies in the railway sector.
These standards are divided into 5 parts entitled as follows:
- Generalities
- Quality specifications and certification of welding manufacturers
- Design specifications
- Manufacturing requirements
- Inspection, testing and documentation
What are the objectives of this standard?
The main objective of EN 15085 is to define specific requirements for welding in the railway industry. It aims to guarantee the quality, safety and reliability of welds used in the manufacture, maintenance and repair of railway components.
Particular attention is paid to the welding of components, railway vehicles and railway parts.
The introduction of these regulations was not prompted by specific accidents. Rather, they meant to improve safety and quality in the railway industry.
It should be noted, however, that incidents in the railway sector have often highlighted the importance of welds quality. This was revealed by the Land Transport Accident Investigation Bureau (BEA-TT) in the course of its investigations…
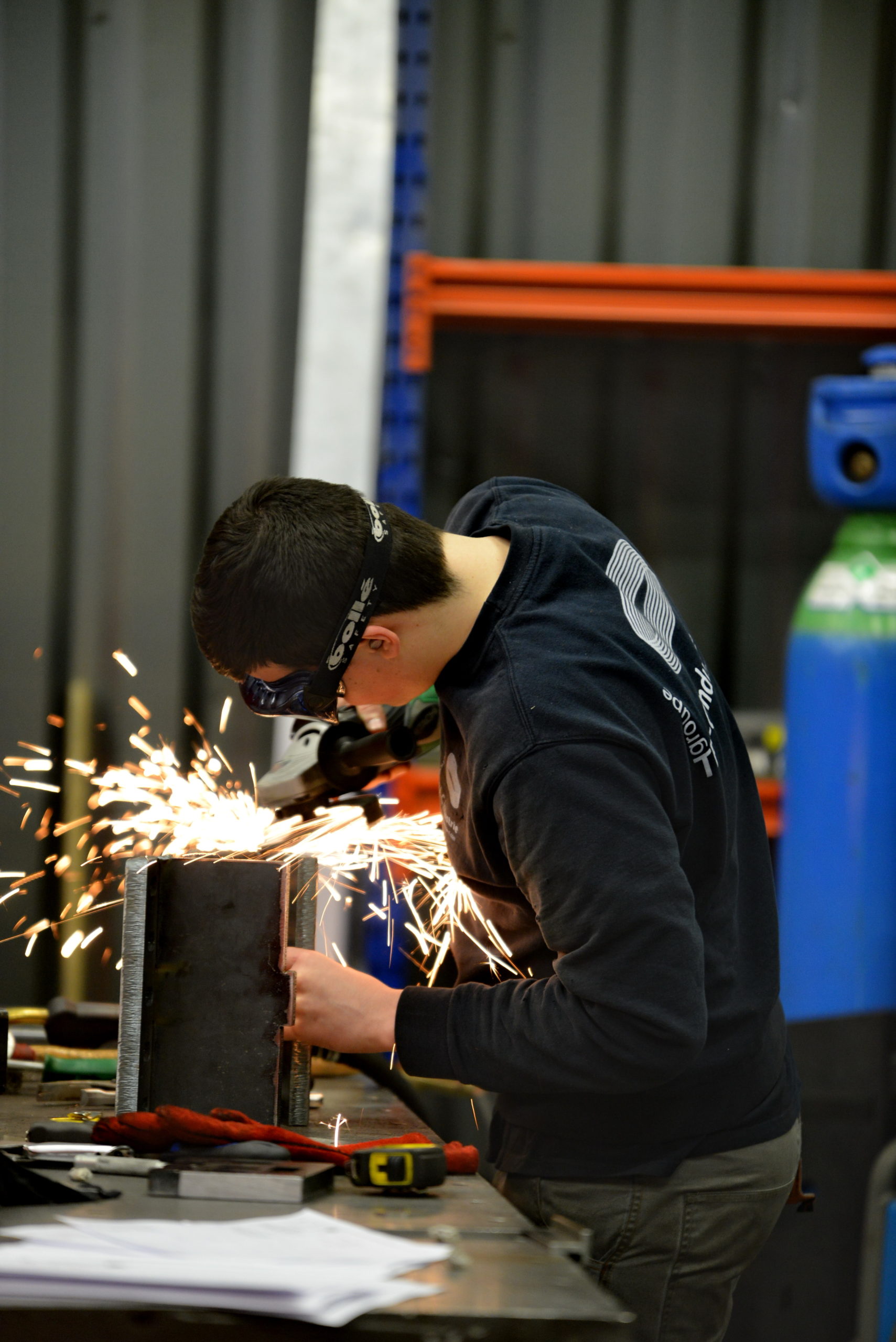
Key points of standard EN 15085
In order to establish a framework for welding operations in the railway sector, EN 15085 covers a number of criteria. They include:
- Areas of application: the regulations apply to manufacturers of railway equipment, maintenance workshops and welding companies involved in the railway industry;
- Classification of welds: EN 15085 uses a classification system to specify the requirements for the different categories of weld. In particular, the complexity of the weld, the size of the weld and the materials used are taken into account;
- Qualification of welders: it establishes criteria for the qualification of welders, including their skills, training and experience;
- Welding processes: the standard also makes it possible to choose appropriate welding processes depending on the materials, welding conditions and quality requirements;
- Inspections and tests: these are requirements for inspections and non-destructive tests to be carried out on welds. This may include visual inspections, radiographic tests, ultrasonic tests, etc.;
- Documentation: ISO 15085 also requires to keep up-to-date documentation on welding procedures, welder qualifications, inspections carried out and test results;
- Maintenance and repair: finally, the standard establishes a framework for operations relating to the maintenance and repair of welds on railway vehicles.
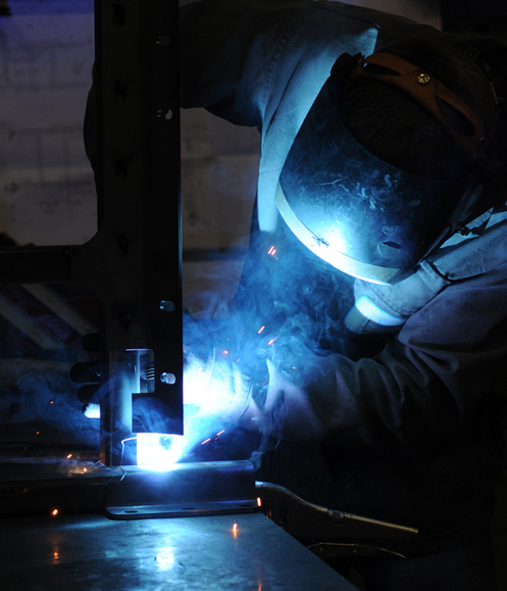
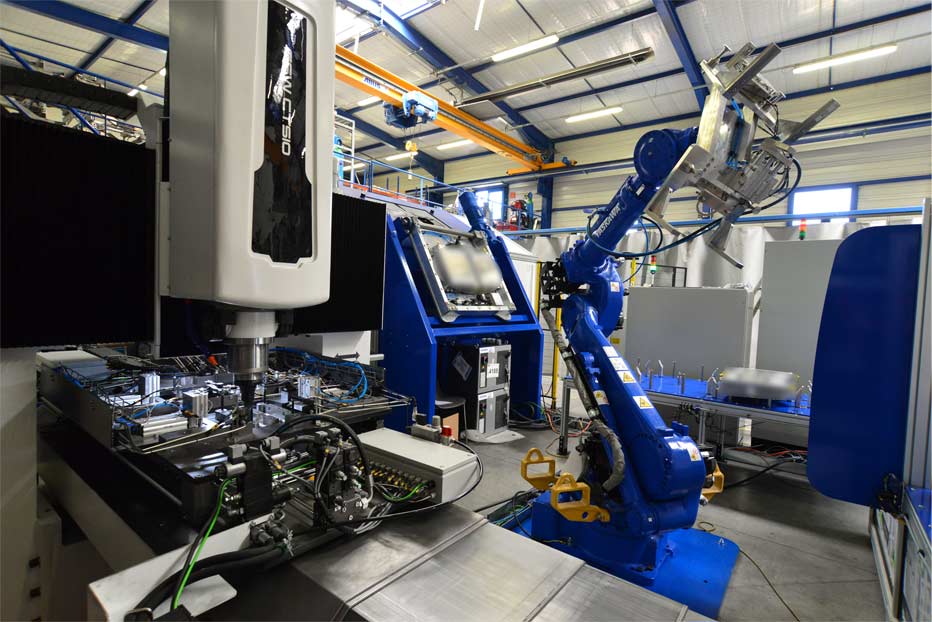
Welding techniques certified to EN 15085
There are several welding techniques that can be EN 15085-certified, provided they meet the various requirements listed above. These include
- Tungsten inert gas welding: an electric arc is created between a continuous wire electrode and the part to be welded. An inert gas is applied to prevent oxidation;
- Arc welding with a coated electrode: in this case, the electric arc is generated between the part to be welded and a fusible electrode, which also serves as a filler metal;
- Submerged arc welding: a free electric arc is generated from a powder poured around a wire electrode, which acts as a filler metal. The parts to be welded melt instantly;
- Friction stir welding (FSW): this solid-state welding process combines the heat generated from the friction of a rotating tool and the pressure exerted on the part to be welded. The softened metal can then be kneaded to form the weld.
An essential reference in the railway industry
The railway industry demands a high level of welding quality for all its components. Particular attention must therefore be paid to vehicle and rail components, to guarantee user safety.
Although EN 15085 standard is not mandatory, it is strongly recommended that manufacturers and industrialists in the railway sector are certified in order to be competitive!
Many customers no longer hesitate to mention this standard in their specifications or contracts. They want to be sure that their operators and welders are qualified.
Apart from the competitive advantage, being EN 15085-certified is also synonymous of know-how and expertise. It demonstrates a certain professionalism as well as a desire to ensure the users safety, a real asset to a company’s brand image…
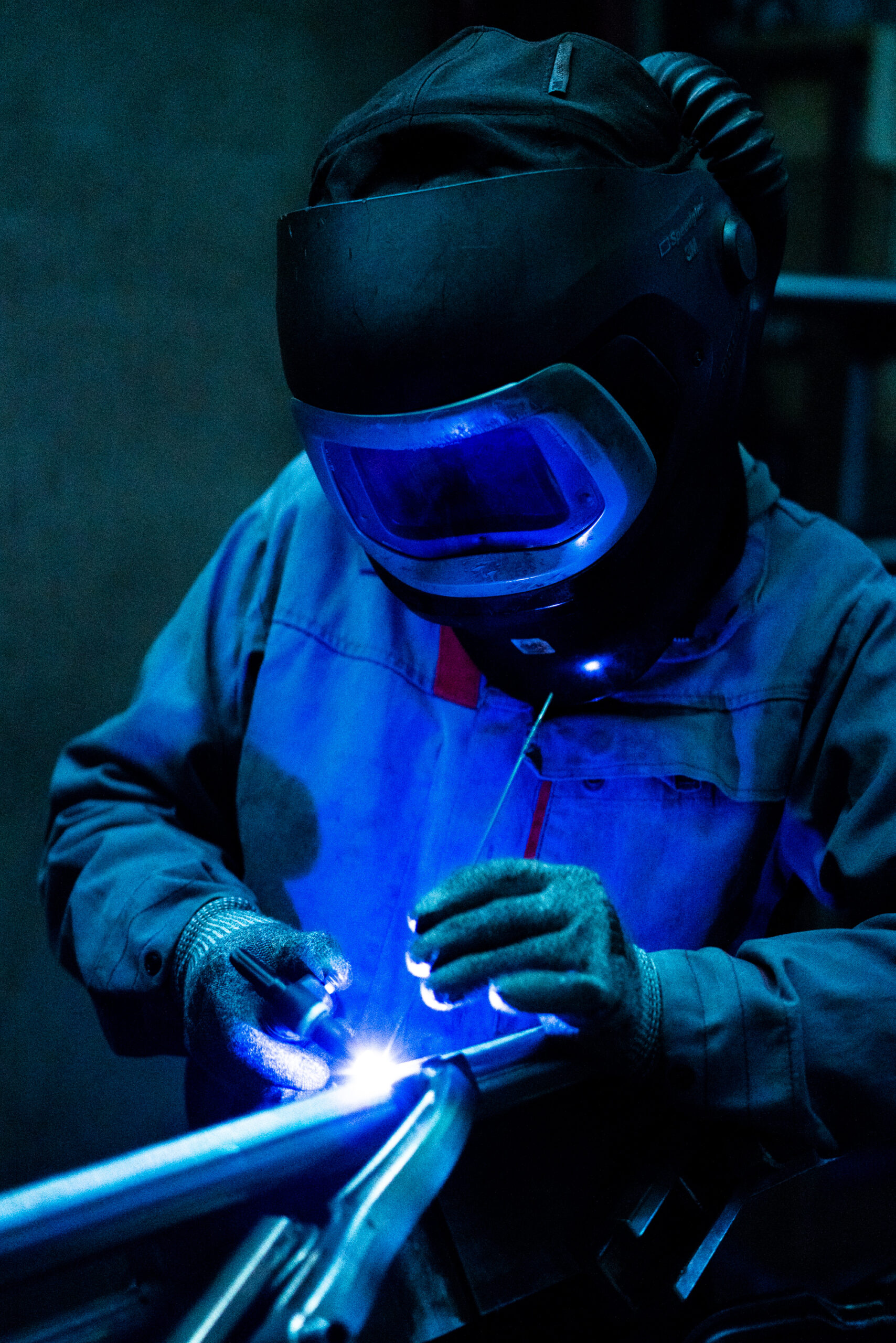
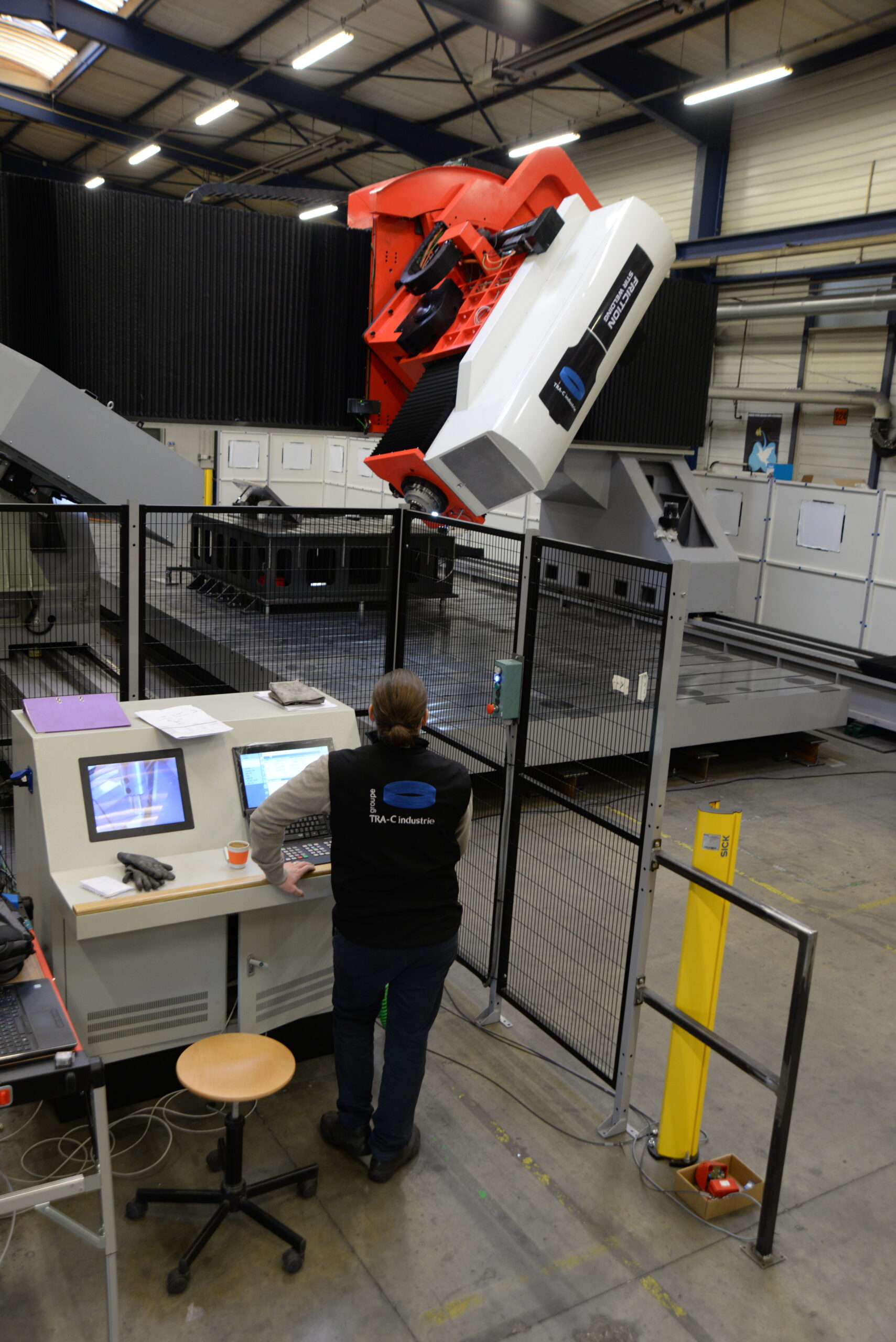
How can you guarantee the quality of your rail welding using the EN 15085 standard?
Companies can be EN 15085-certified from a private entity. An audit will thus be carried out to assess the skills required. The certification will then be issued if the requirements are met.
Because of the importance of this accreditation, particularly in terms of safety, certification is broken down into several levels, from CL1 to CL4. Companies meeting all the criteria are awarded the CL1 level.
If, as a manufacturer, you cannot or do not wish to obtain this certification, it is preferable to contact a qualified EN 15085-certified subcontractor.
It is the guarantee to work with professional welders and operators who care about the quality of their welds. You’ll also ensure that you are compliant with specifications and that regular, meticulous checks are undertaken…
Serinox, welding specialist for the rail industry
EN 15085-certified, Serinox is now a renown player in the railway sector. The company has the experience and know-how needed to build locomotives and produce standardised railway rolling stock.
Committed to quality, Serinox, a subsidiary of the TRA-C industrie group, is CL1-certified from the Institut de Soudure since 2016. The company is listed in the European register.
To ensure optimum quality and meet the specific needs of the railway industry, we guarantee to our customers:
- Regular audits (production, welding stations, etc.)
- Strict adherence to deadlines
- Satisfaction surveys
- Frequent testing of our products (waterproofing, crash-testing)
- Follow-up from the material (sheet metal-tube) to the part (numbering possible)
- Recognised expertise in the manufacture and transformation of metals
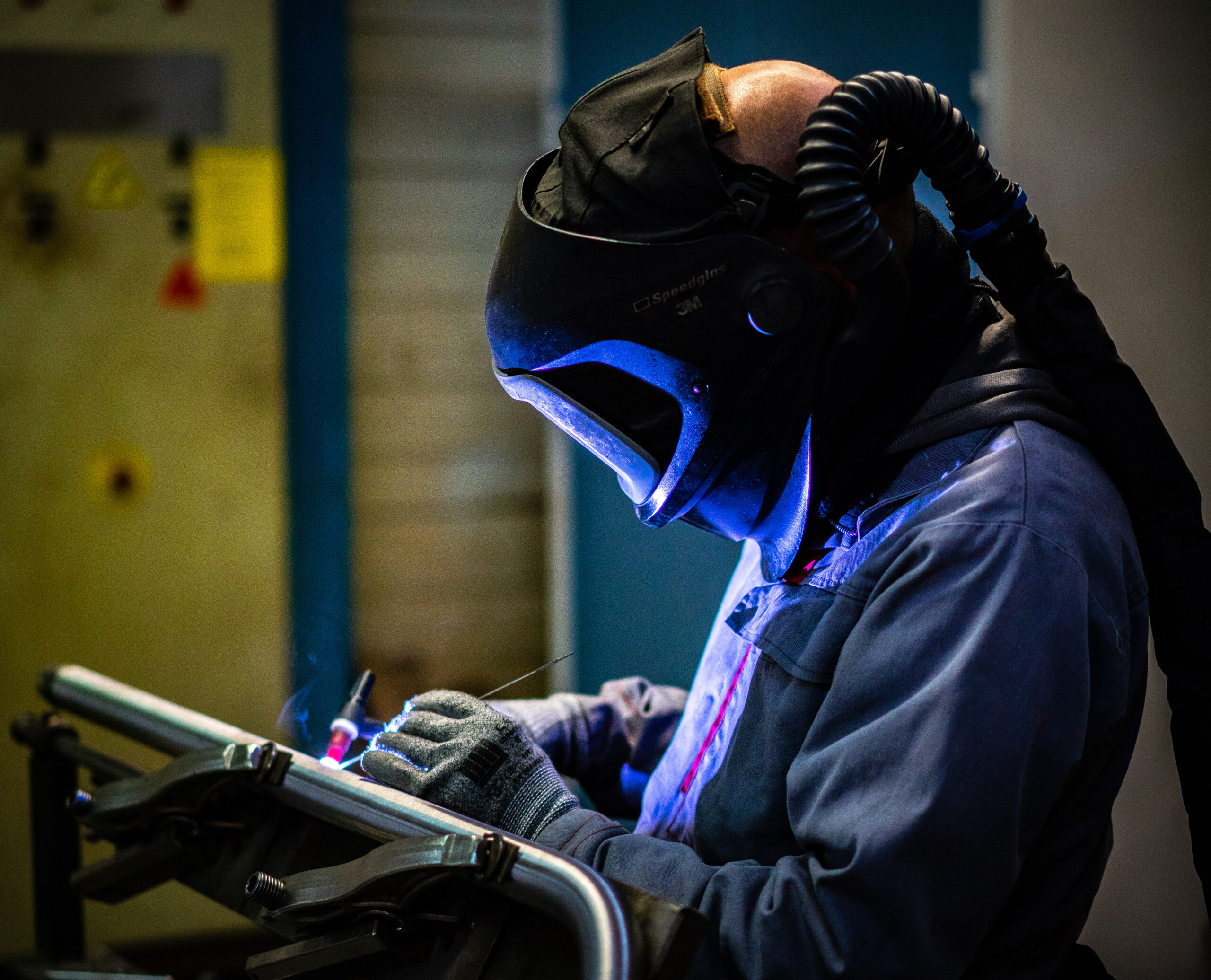
Do you want to find out more about ISO 15085? Would you like to be guided by a certified company to carry out your welding manufacturing projects for components, railway vehicles and parts?