EN 9100 standard and welding in the aerospace industry
Today, welding in the aerospace industry plays an essential role in civil and military aviation. It guarantees the structural integrity of components, the reliability of parts and the safety of passengers…
High mechanical stress, extreme temperature and pressure conditions, high economic stakes… Because of the constraints specific to the aerospace sector, the industry is governed by numerous regulations.
Amongst them, there is the EN 9100 standard, “Quality Management Systems in the Aerospace and Defense Sector“. In the aeronautics industry, this certification is now a real guarantee of assurance and quality!
But what are the challenges facing the aerospace industry? What is the EN 9100 standard? And what are the welding requirements in this sector? In this article, TRA-C industrie tells you more about welding in the aerospace industry …

Particularities of the aeronautics and space sector
Because of its constraints, the aeronautics, space and defense sector (ASD) is very special. These include:
- Human safety: human lives are at stake, whether on planes or other aircraft. Therefore, passenger safety remains the top priority in this sector;
- Strict regulations: the aerospace industry is heavily regulated by the Consequently, companies are required to obtain numerous certifications;
- Technical complexity: the design, manufacture and maintenance of aircraft, shuttles, satellites and launchers also require solid technical skills;
- Long service life: aerospace equipment remains in service for several decades. Materials and systems must therefore be durable;
- International supply chain: quality management must be ensured at all levels, from component suppliers to final assembly;
- Regular checks: any modification or repair to electrical parts or systems must also be carefully documented, assessed and approved;
- Component reliability: parts and systems have to operate in extreme environments. It is therefore essential that they are resistant;
- Evolving technologies: rapid technological advances mean that companies in the sector must constantly adapt.
What is the EN 9100 standard?
The EN 9100 standard is part of a series of international regulations defined by the International Organisation for Standardisation (ISO). It governs the requirements for quality management systems in the aerospace and defense industries.
Based on the ISO 9001 standard, it includes additional requirements specific to the aerospace, civil and military sectors. Its aim is to guarantee the safety, quality and reliability of parts for aerospace devices and systems…
Adopting the 9100 standard is often a prerequisite for companies wishing to work with major players in the aerospace industry, such as aircraft manufacturers, first-tier suppliers and prime contractors.
This comprehensive certification covers around 400 criteria to maintain high standards throughout the supply chain. It also ensures the conformity of welding in the aerospace industry!
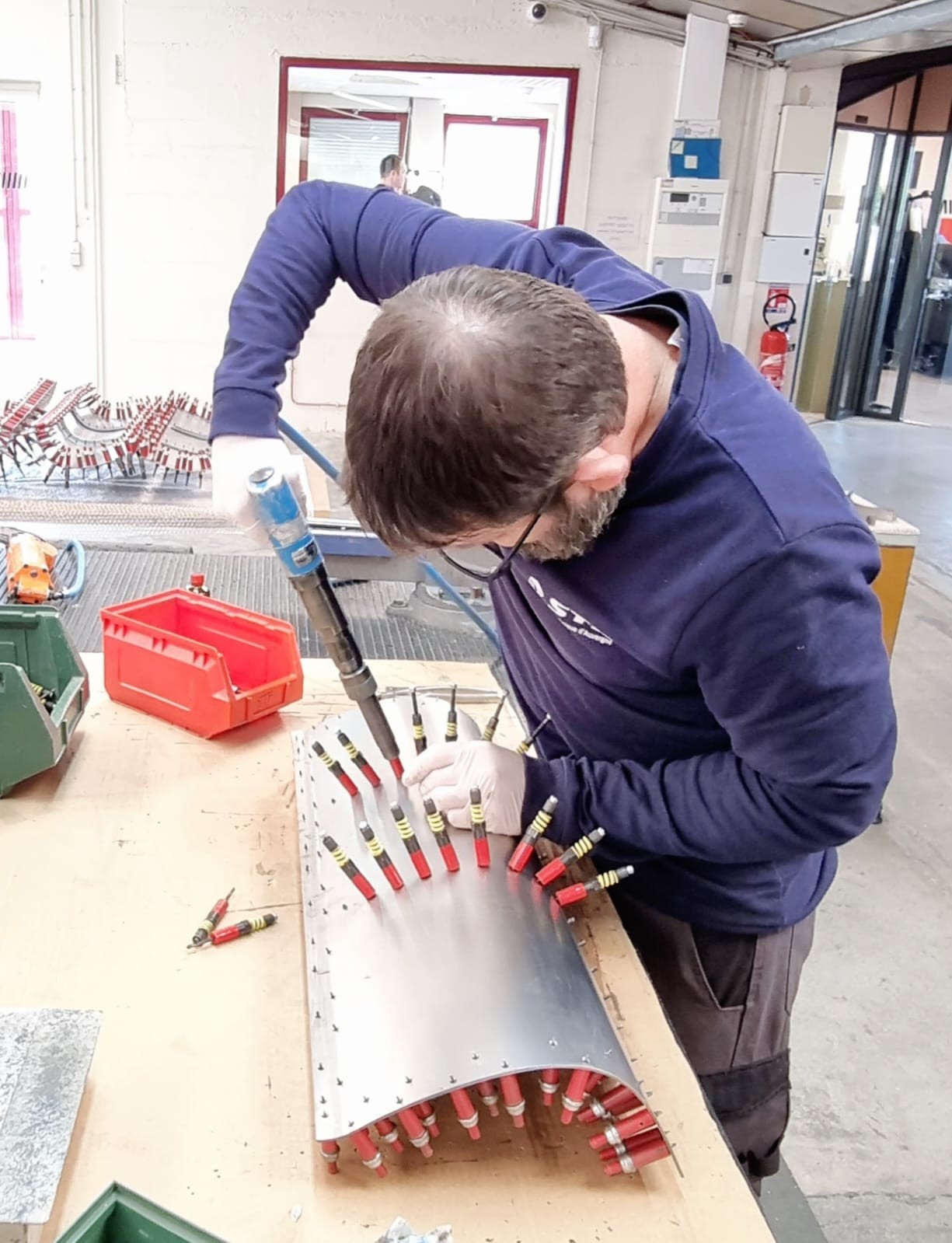
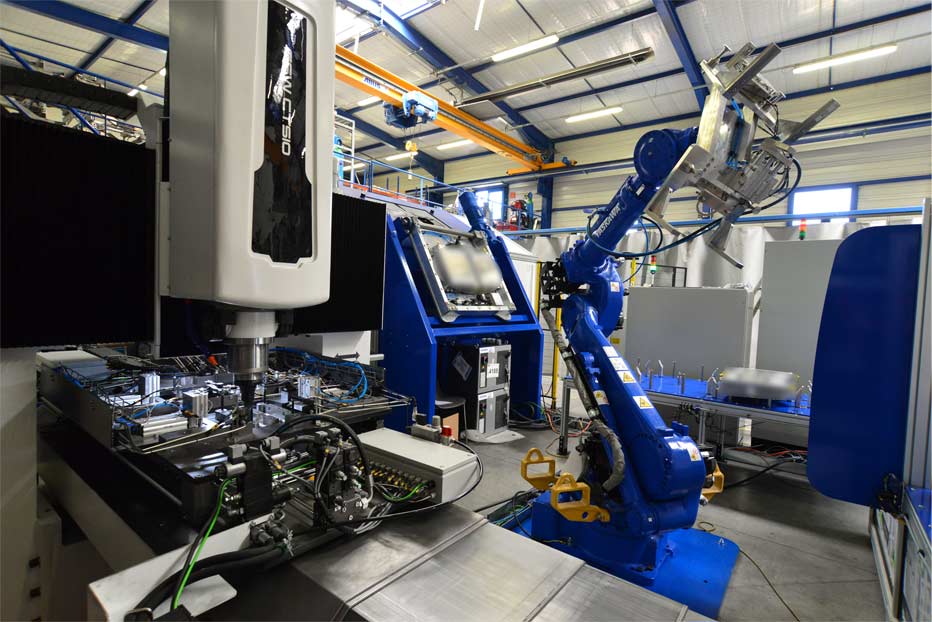
What are the objectives of the EN 9100 standard?
The EN 9100 standard was developed to meet the specific needs and rigorous expectations of the aerospace industry. It has a number of objectives:
- Quality improvement: perfecting manufacturing and welding processes and enhancing the performance of organizations in the aerospace sector;
- Regulatory compliance: ensuring compliance with regulations and standards applicable to the civil and military aviation as well as the space industry;
- Risk management: identifying, assessing and managing the risks associated with operations and processes that may affect passenger safety or component quality;
- Uniformity in the supply chain: promoting the adoption of consistent and compatible quality management practices between the various players;
- Traceability: tracking materials throughout the design, manufacturing, delivery and welding process in the aerospace industry;
- Anticipating defects: implementing preventive measures to reduce errors and non-conformities. This starts with the welding of components.
Welding requirements in the aerospace industry
In order to guarantee the quality and safety of both components and passengers, EN 9100 defines strict criteria for all manufacturing processes. Welding operations must therefore comply with this standard!
Vibration, aerodynamic forces, variations in temperature and pressure: aircraft and space vehicles are subjected to extreme stress. Welding in the aerospace industry has to guarantee the durability and reliability of structures.
In the aerospace field, certain materials and metal parts cannot be welded or brazed. It is therefore essential to master the welding process, or to call in a specialist company to design, manufacture or weld components.
Finally, welds should be regularly inspected using non-destructive testing methods to detect any anomalies or potential defects. These techniques include radiography, ultrasound and visual inspection…
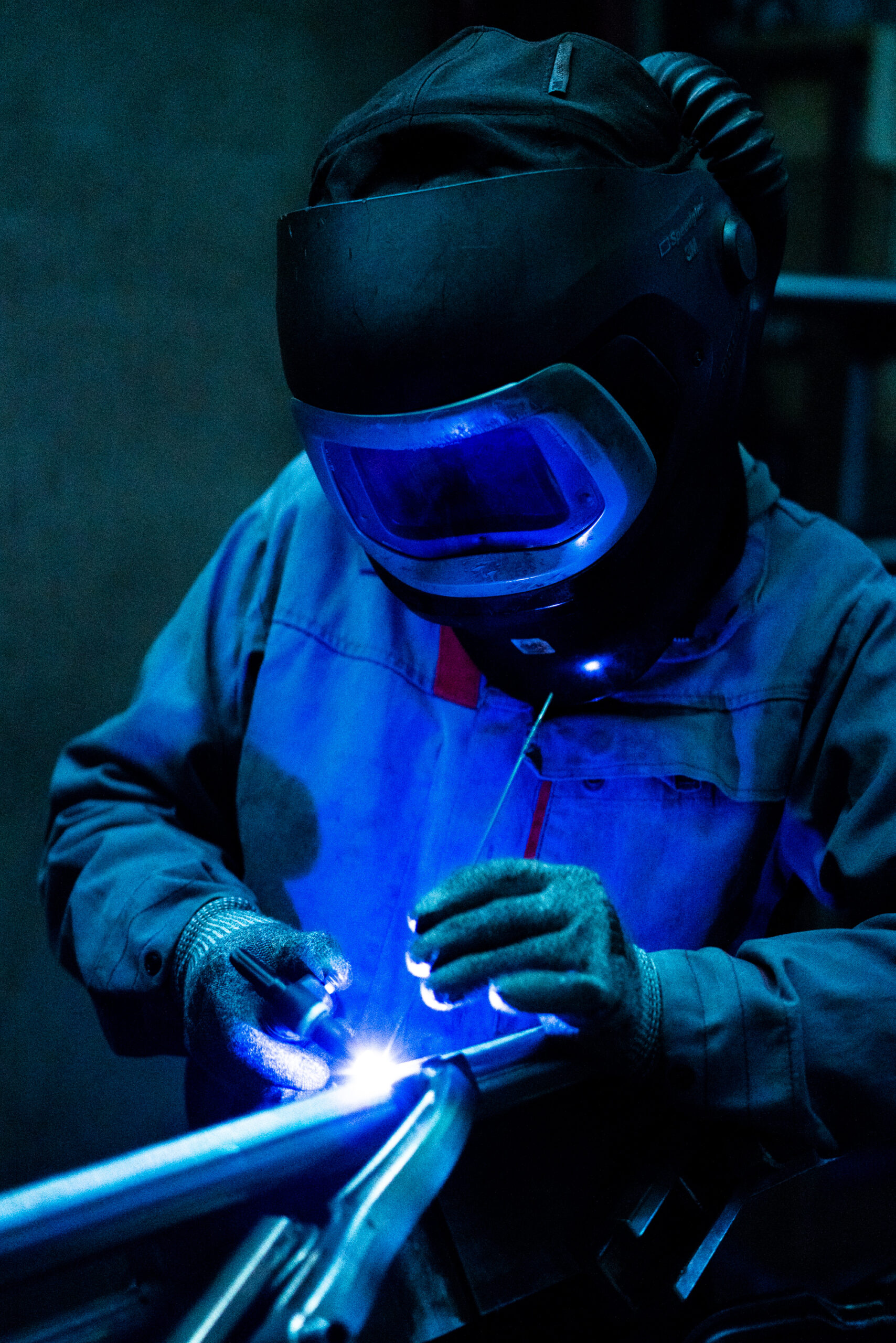
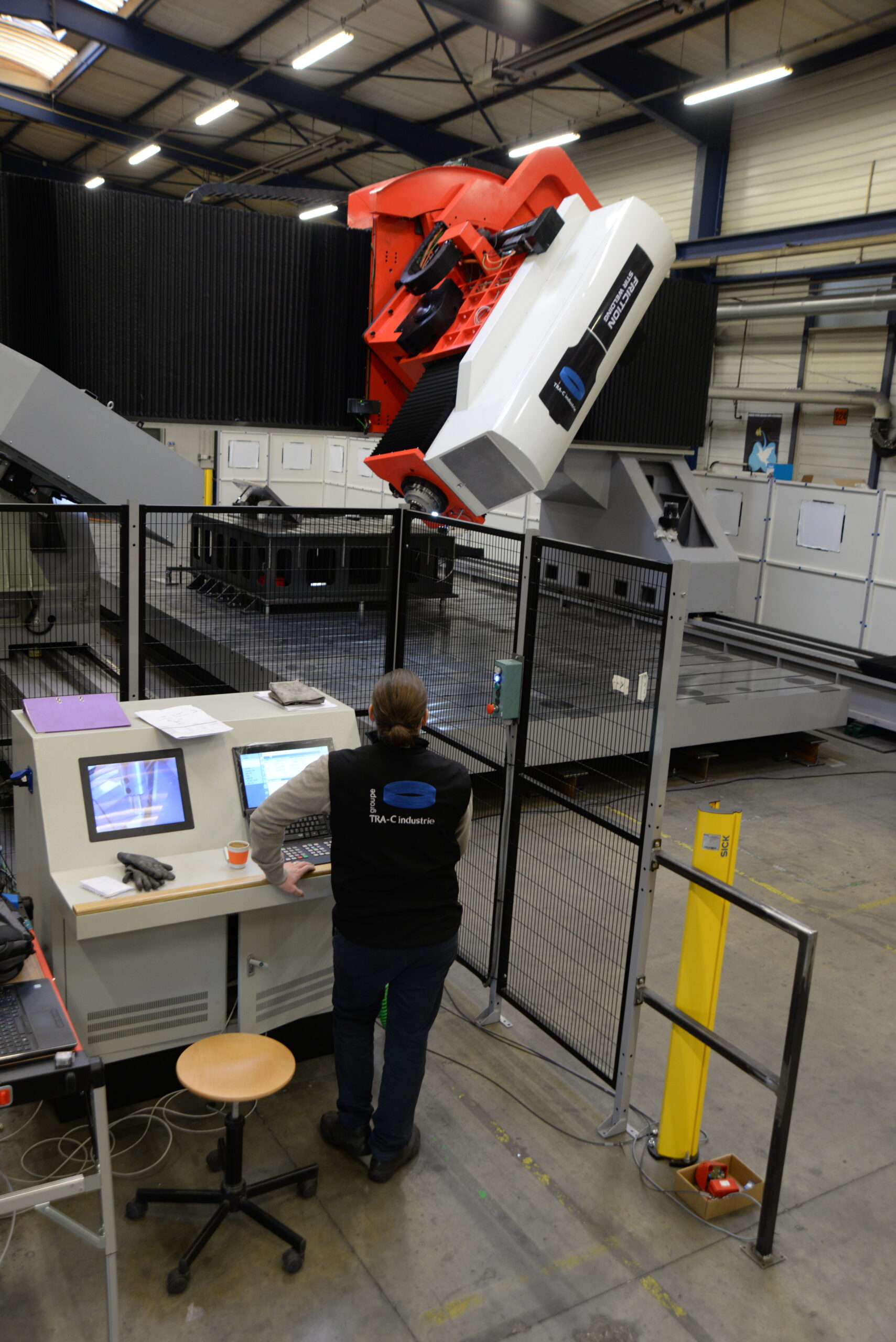
The advantages of welding in the aerospace industry
By meeting all these requirements, welding in the aerospace industry offers many advantages:
- Lighter components: first of all, welding makes structures This is essential for reducing the weight of aircraft and space vehicles, and thus improving their power efficiency;
- Customised structures: welding also offers the flexibility needed to create complex structures. In this way, it meets the specific design requirements of aircraft and satellites;
- Structural integrity: well-executed welded joints are highly This means that components can withstand extreme mechanical stress and environmental conditions;
- Production efficiency: welding also speeds up the manufacturing process. This is an important parameter in an industry where production speed has a direct impact on competitiveness and delivery times;
- Adaptability to materials: the aerospace industry uses specific materials such as light alloys, composites and superalloys. Welding assembly methods are compatible with these materials;
- Structural repairs: welding finally enables damaged or worn components to regain their functional integrity. It is therefore useful for repairs.
The different EN 9100-certifiable welding processes
Working on and assembling aeronautical parts requires a strong expertise. Welding in the aerospace industry must consequently meet the requirements of the EN 9100 standard.
One example is friction stir welding (FSW). This solid-state welding process can be used to join light alloys and a variety of materials such as aluminium. Ecological and economical, it is one of the most reliable techniques.
TIG welding, an arc welding method, also offers excellent assembly quality. It is therefore suitable for welding aeronautical parts. It can be used to weld thin layers as well as heterogeneous and homogeneous materials.
MIG welding is another form of arc welding that uses a consumable wire and an inert gas to join two parts. Fast and efficient, this semi-automatic welding technique lends itself well to applications in the aerospace sector.
Finally, MAG welding also requires a gas to feed the electrode, except that the gas is active. Used for assembling steel panels, this process is useful for applications in the aerospace market and other large-scale manufacturing sectors…
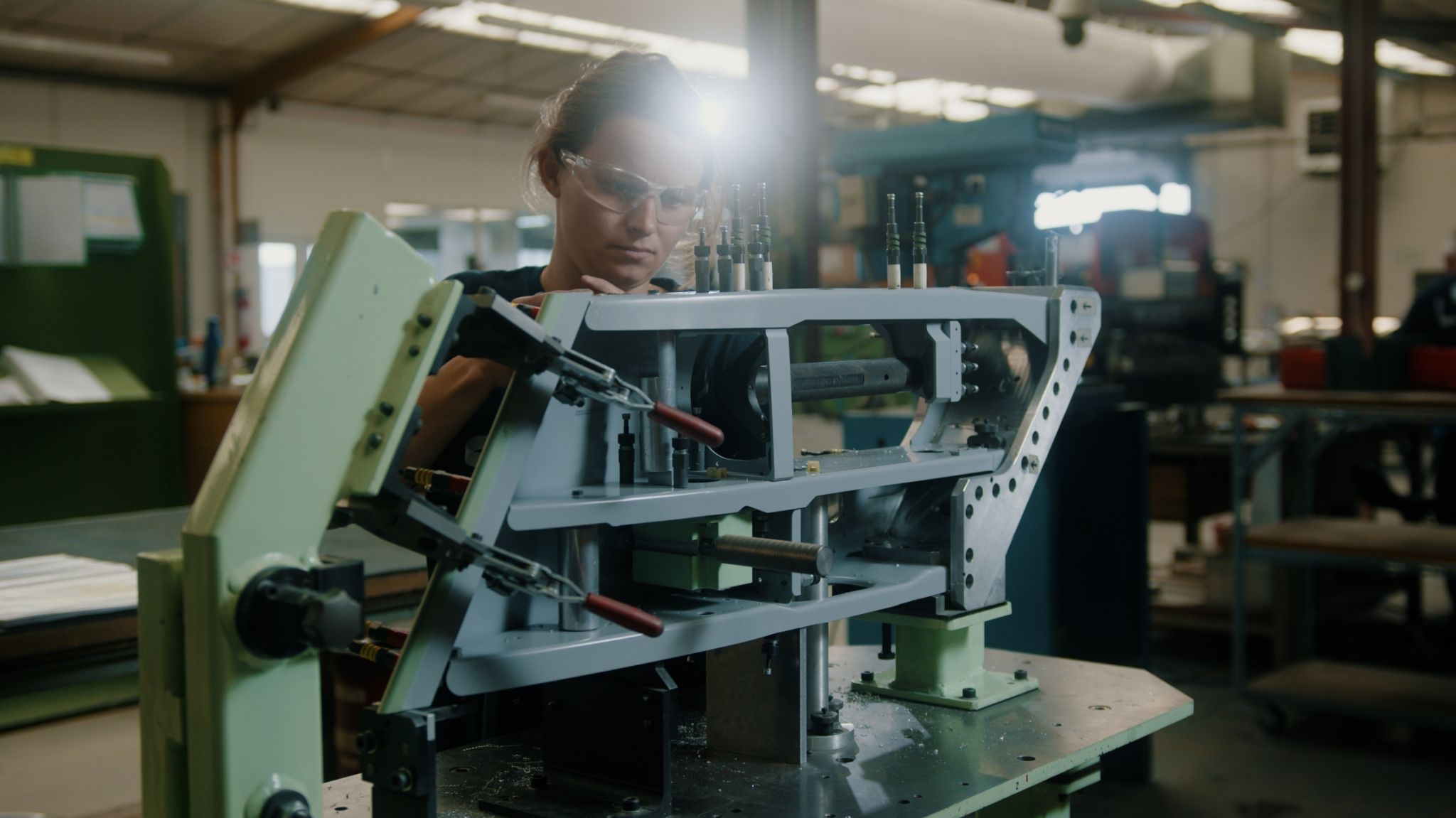
Jacques Soudure, expert in welding for the aerospace industry
Based in Issoudun (36), Jacques Soudure, a subsidiary of the TRA-C industrie group, specialises in fine precision sheet metal work. With a recent fleet of 2,100 m2 and digital machines, the company supports manufacturers in the manufacture of small and medium-sized production runs.
Certified to EN 9100, Jacques Soudure is officially referenced on the “OASIS” database by the aeronautics, defence and space industries. It is also a supplier to major manufacturers in the sector, such as Safran, Thalès and Stelia.
Our solid expertise in industrial sheet metal work enables us to produce complex parts or assemblies combining several trades: sheet metal work, welding, machining, painting, assembly, etc.
Ets Glaude is an expert in fine precision sheet metal work for the aerospace industry. Also EN 9100 certified and based in Châteauroux, this other subsidiary manufactures assemblies and sub-assemblies for civil and military aircraft.
With its solid expertise, cutting-edge welding techniques and commitment to continuous improvement, the company is in a position to advise major contractors such as Dassault Aviation, and to be involved at every stage of their projects!
Are you an aerospace manufacturer? Would you like support with your welding projects in the aerospace industry? Jacques Soudure and Ets Glaude are at your side, from design to manufacture of fully customised components: