What are the differences between boilermaking, ironworking, and metallurgy?
Boilermaking, ironworking, and metallurgy are three trades that are closely related to each other, yet they involve distinct tasks, skills, and tools. All three trades involve working with metals, but they each have unique applications and require different levels of expertise.
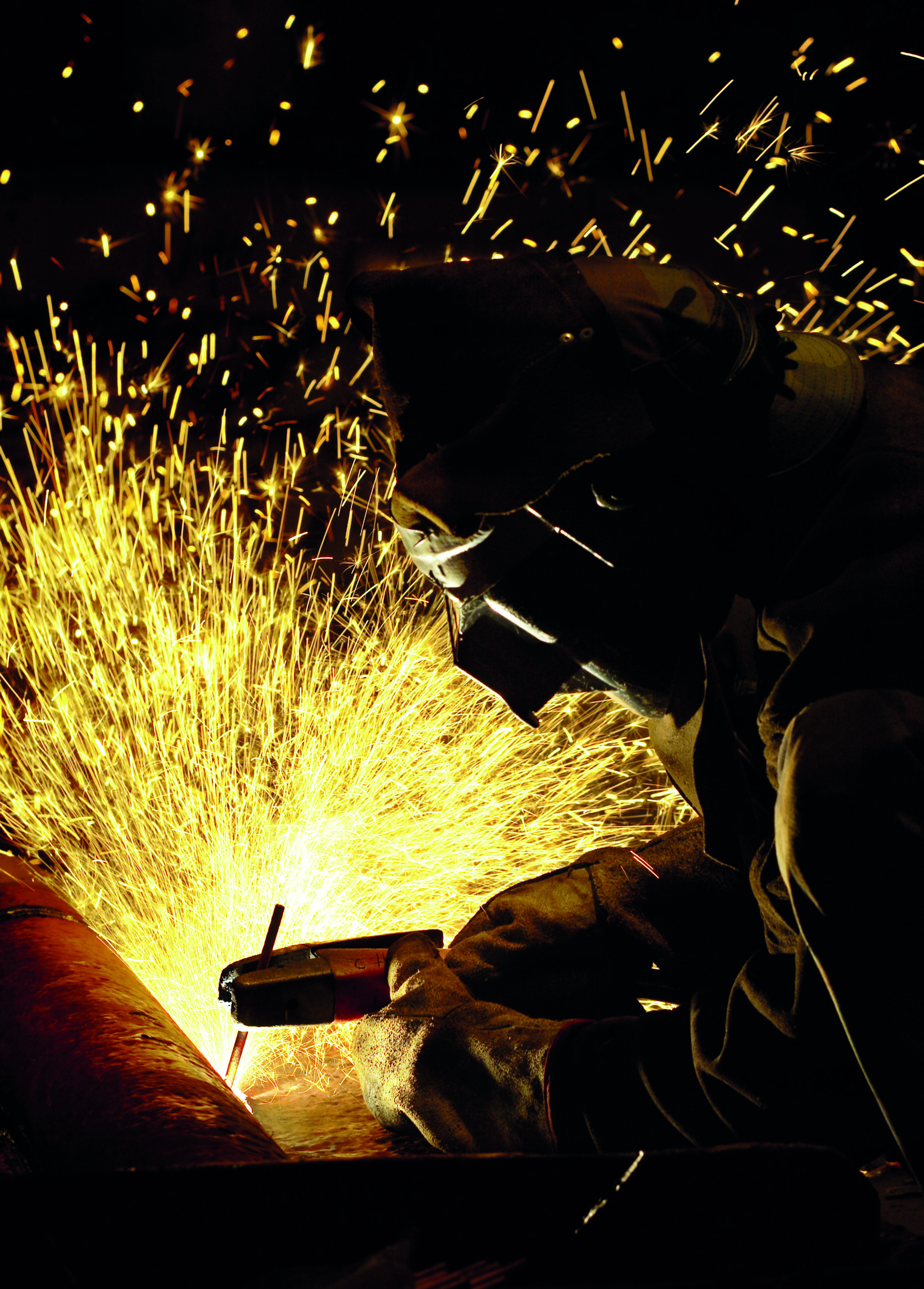
Metallurgy
Metallurgy is the study of metals and their properties. Metallurgists use their knowledge of metal properties and behavior to develop new materials and improve existing ones. They work in a variety of industries, including manufacturing, mining, and aerospace.
Metallurgists use a range of techniques to analyze metals and alloys, including X-ray diffraction, electron microscopy, and thermal analysis. They also develop and test new materials, such as super alloys, which are used in high-temperature environments. Metallurgists play a critical role in ensuring the quality and safety of metal products.
Versatility
One of the most significant differences between metallurgy and the other two disciplines is the focus on research and development. Metallurgists spend a significant amount of time in laboratories, testing and analyzing metals to understand their properties and behavior. While they may work on specific projects, such as developing new alloys for aircraft engines, their work is focused on the broader field of metallurgy.
Another difference between metallurgy and boiler making or ironworking is the level of education and training required. Metallurgists typically have advanced degrees in materials science or a related field, while boilermakers and ironworkers generally learn their trade through apprenticeships or vocational training programs.
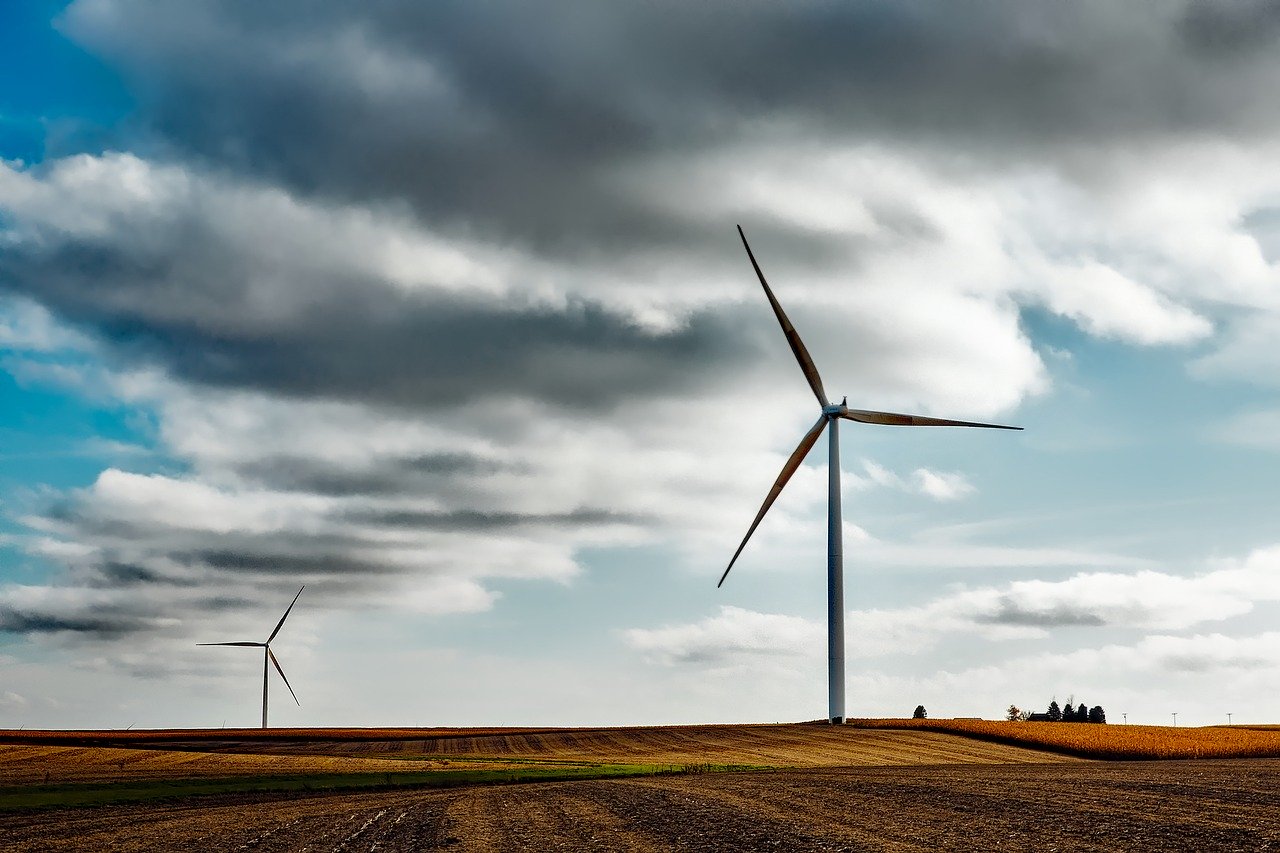
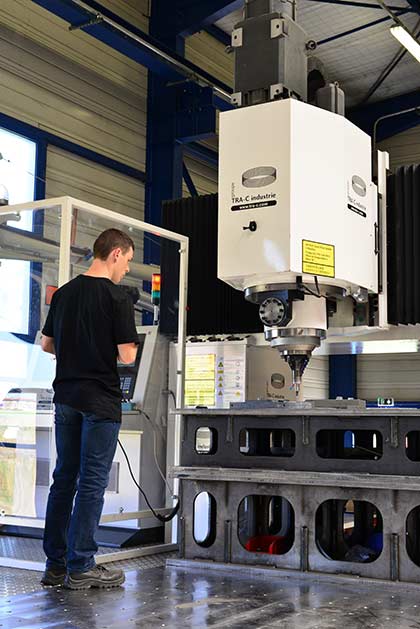
Forge
Forging is an ancient craft that consists of working iron. Thus, blacksmiths were once responsible for making tools, weapons and other iron objects. Traditional blacksmithing was already an important technique in antiquity and has continued until today: blacksmiths still produce handmade products with traditional techniques and tools.
Iron work requires a great deal of skill and experience. The blacksmith must heat the material and then give it the desired shape using a hammer. However, with industrialization, the craft of blacksmithing was increasingly replaced by machine-made products.
In the process of industrial forging, metals are transformed on a large scale in factories and factories. Thanks to modern mechanical processes and technologies, it is possible to produce larger quantities in less time.
Industrial forging is used in many fields, for example for the manufacture of parts for the automotive industry, the construction of bridges and buildings, as well as for the manufacture of tools and machines. It is also used to make special parts such as bolts, nails, rings and other castings.
A more efficient process
Unlike traditional forging, where the blacksmith works the metal manually with a hammer, industrial forging uses presses and stamping machines. These processes make it possible to produce parts faster and more efficiently and to work on complex shapes with tight tolerances.
Industrial forging has played a decisive role in economic development and is now a mainstay of modern manufacturing industry. It allows companies to produce larger quantities in less time, resulting in increased productivity and profitability.
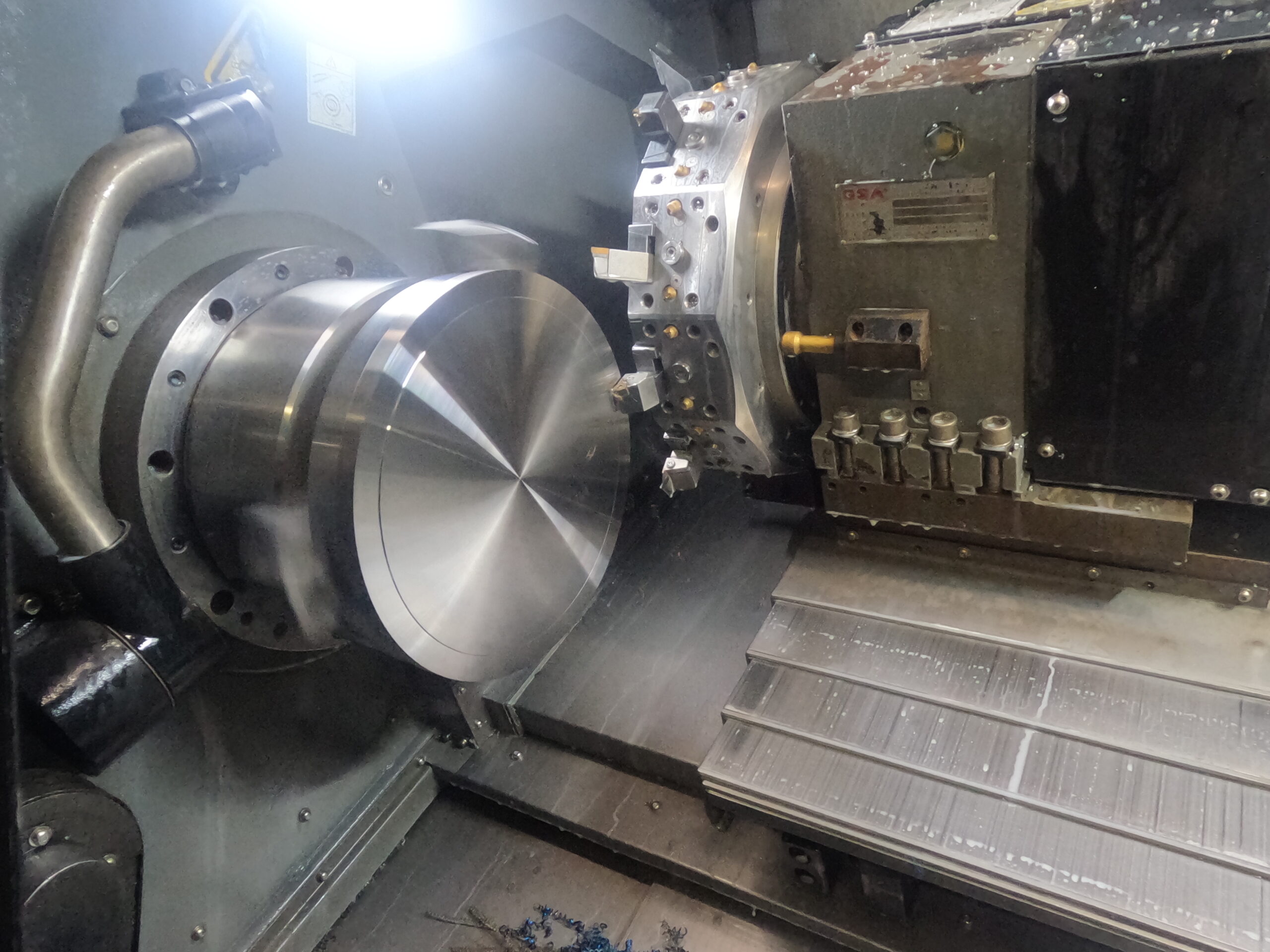
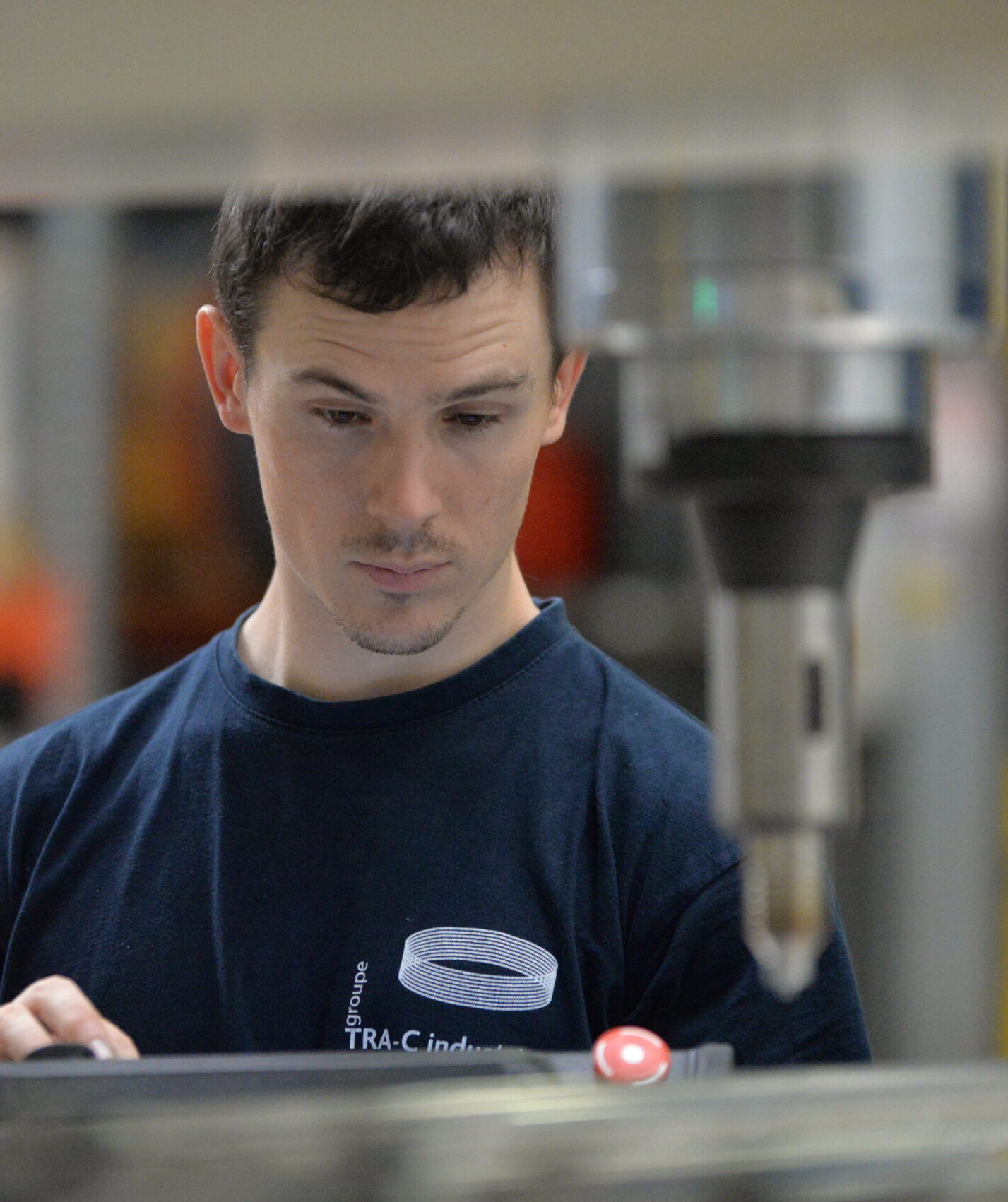
Ironwork
Iron is a sturdy material that can withstand loads for a long time and, together with an appropriate protective layer, can also become resistant to weather and corrosion. Iron working is an umbrella term for all processes in which a ferrous product is modified or shaped. This can be done by forging, milling, turning, drilling, stamping or casting.
Iron working is an important component of metal processing and is used in many fields such as the automotive industry, mechanical engineering and the building industry. Depending on the requirements and objectives of the project, iron processing can be done by hand or with modern tools and machinery.
Boilermaking
Boilermakers typically work with heavy steel plates, which they cut, shape, and weld together to create the various parts of a boiler. They also install pipes, valves, and other components to ensure that the boiler functions properly. Boilermakers must have a strong understanding of mechanical and electrical systems, as well as safety protocols.
One of the most significant differences between boilermaking and other engineering disciplines is the focus on constructing boilers. Boilermakers may work on other projects, but the bulk of their work revolves around the design and construction of boilers.
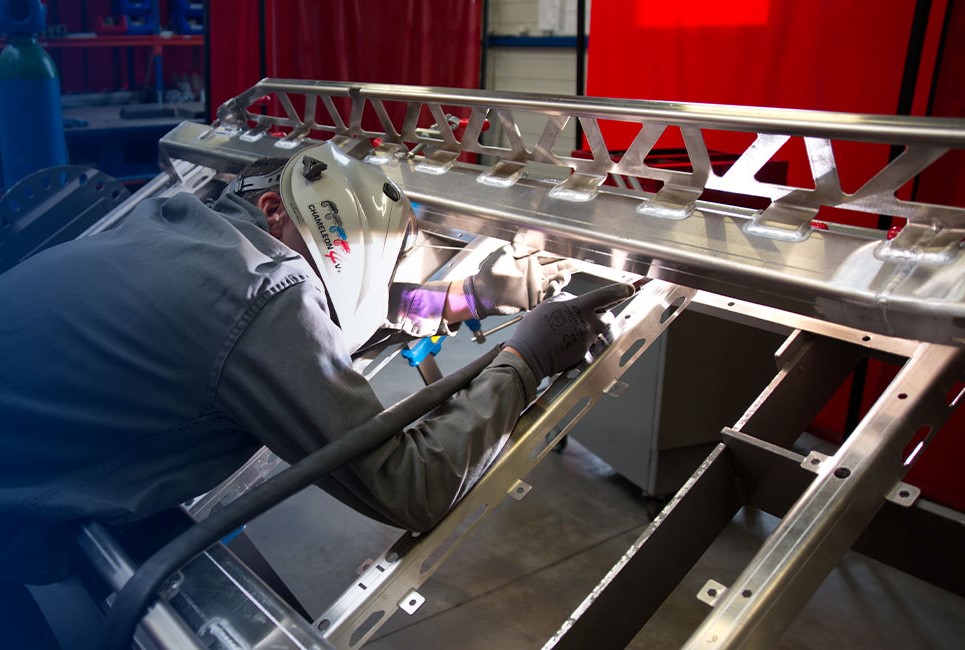
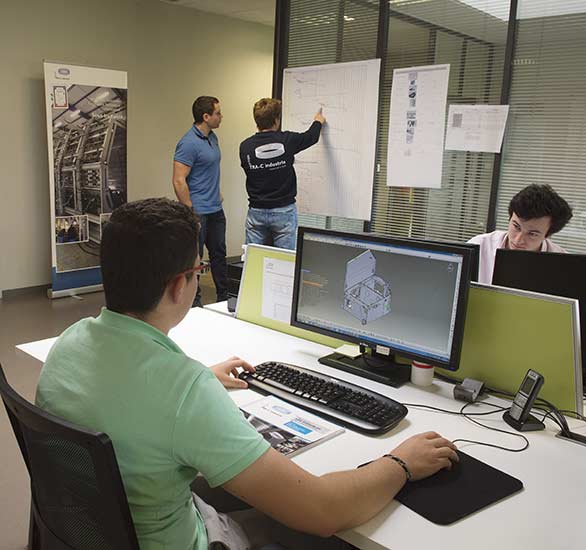
Conclusion
In conclusion, boilermaking, ironworking, and metallurgy are three trades that involve working with metals, but each trade has unique applications and requires different levels of expertise. Boilermaking focuses on the construction, installation, and maintenance of large containers used for storing and transporting liquids and gases. Ironworking focuses on the fabrication and installation of structural steel and other metal components in building construction.
Metallurgy is a scientific field that studies the properties, production, and uses of metals, and plays a crucial role in developing new materials and processes. While there are some overlaps between these trades, each requires a different set of skills, tools, and knowledge. By understanding the differences between these trades, we can appreciate the diversity and complexity of the metalworking industry and the important role it plays in our economy and society.