Focus on TIG welding: what you need to know
Among the various arc processes, TIG welding offers one of the finest assembly qualities. You can use it on all metals, homogeneous and heterogeneous, and it also allows continuous working at weld points on all thicknesses up to the thinnest. So what is the principle of TIG welding? What are the specificities and applications of TIG welding? Here’s everything you need to know about TIG welding.


The principle of TIG welding
TIG, or Tungsten Inert Gas, otherwise known as GTAW (Gas Tungsten Arc Welding) in the United States, lives up to its name: it uses a tungsten electrode and an inert gas. The principle, in itself, is simple. TIG welding involves harnessing the energy generated by an electric arc that melts the materials to join them. A few elements are required to achieve this:
- The TIG welding machine, connected to the elements to be assembled and to the welding torch.
- The tungsten electrode inserted in the torch; this electrode does not fuse, so it won’t melt or wear out.
- A neutral gas, which protects the weld from corrosion, molten metal being subject to oxidation.
- A trigger, which simultaneously controls the input of gas and the cut-off of the electric current.
- A rod, if welding with filler metals.
The connected part is earthed. As soon as the trigger is actuated, it releases the gas and closes the electrical circuit, causing the current to flow. When the electrode is close enough (at least 5 mm from the part), the electric arc shoots out. It emits energy powerful enough to melt metal. The two base metals mix; this is known as the melt-pool.
At the same time, the robot or the welder brings in metal, which also melts and, in turn, mixes with the melt-pool. By mixing with the molten material, it enlarges it, which creates the weld bead.
While the principle described is simple, several parameters are involved in achieving a high-quality result.
The parameters to be taken into account
The type of metal or alloy of essential elements such as filler metal and their size; thin sheet metal, for example, has specific features.
- The choice of electrode;
The TIG welding speed, i.e. the rate at which the welder progresses, determines the weld bead’s cleanliness.
- The flow, whether the flow of the gas or the flow of the filler metal.
- The welding angle and position, which determines the performance of the connection.
TIG welding here reveals its complexity and the essential dexterity required to carry out the process. It can be automated, in full or in part, to free up welders and make their work easier.

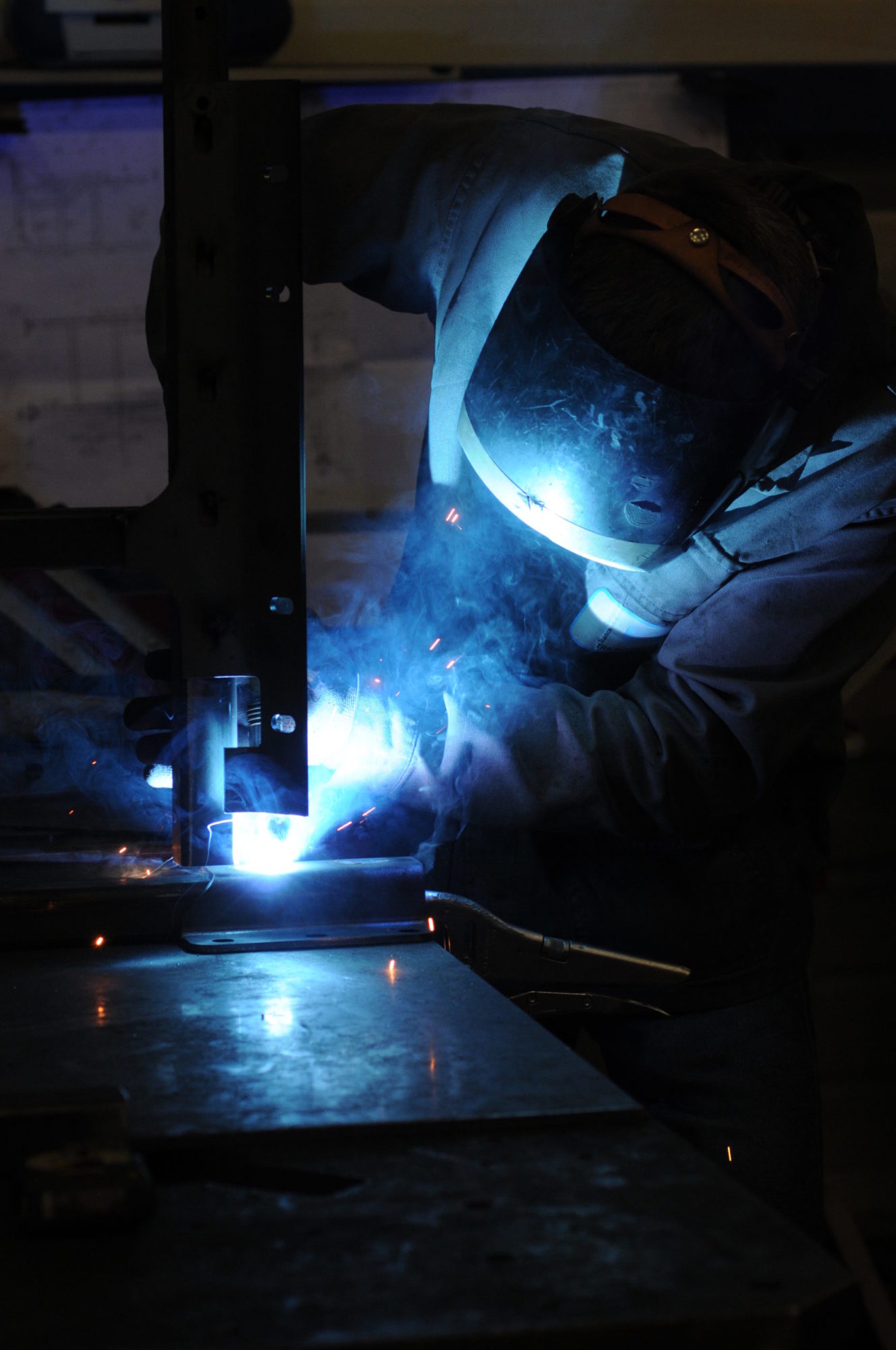
Variants of TIG welding
Depending on the nature of the metal to be assembled, the dimensions and thicknesses to be connected, the intensity used is of great importance. The generator, which produces the electric current, also serves as a control unit to be adapted as needed.
– AC / DC welding
AC (alternating) current is more suitable for working light metals such as aluminium because it increases the penetration of the melt-pool by removing the alumina layer. On the other hand, DC (direct) current with direct polarity is ideal for heavy metals, stainless steel, carbon steel or even copper. It allows more refined management of the energy supplied.
– Pulsed welding (ATIG)
Pulsed welding limits the energy use during TIG welding, using a finely tuned current that alternates peak current and base current. This variant reduces the amount of molten metal and is very useful for assembling thin and delicate parts with regularity and without degrading them.
What are the applications of TIG welding?
TIG welding is very popular because it produces extremely precise results. Seams achieve high quality with good mechanical performance. It provides the opportunity to work on all alloys and metals, particularly stainless steel, which is very hygienic and resistant to shocks and thermal shocks, and aluminium, which is light, malleable, and resistant to corrosion. It also has a significant advantage: it allows work on thin sheets. Extended applications of TIG welding are:
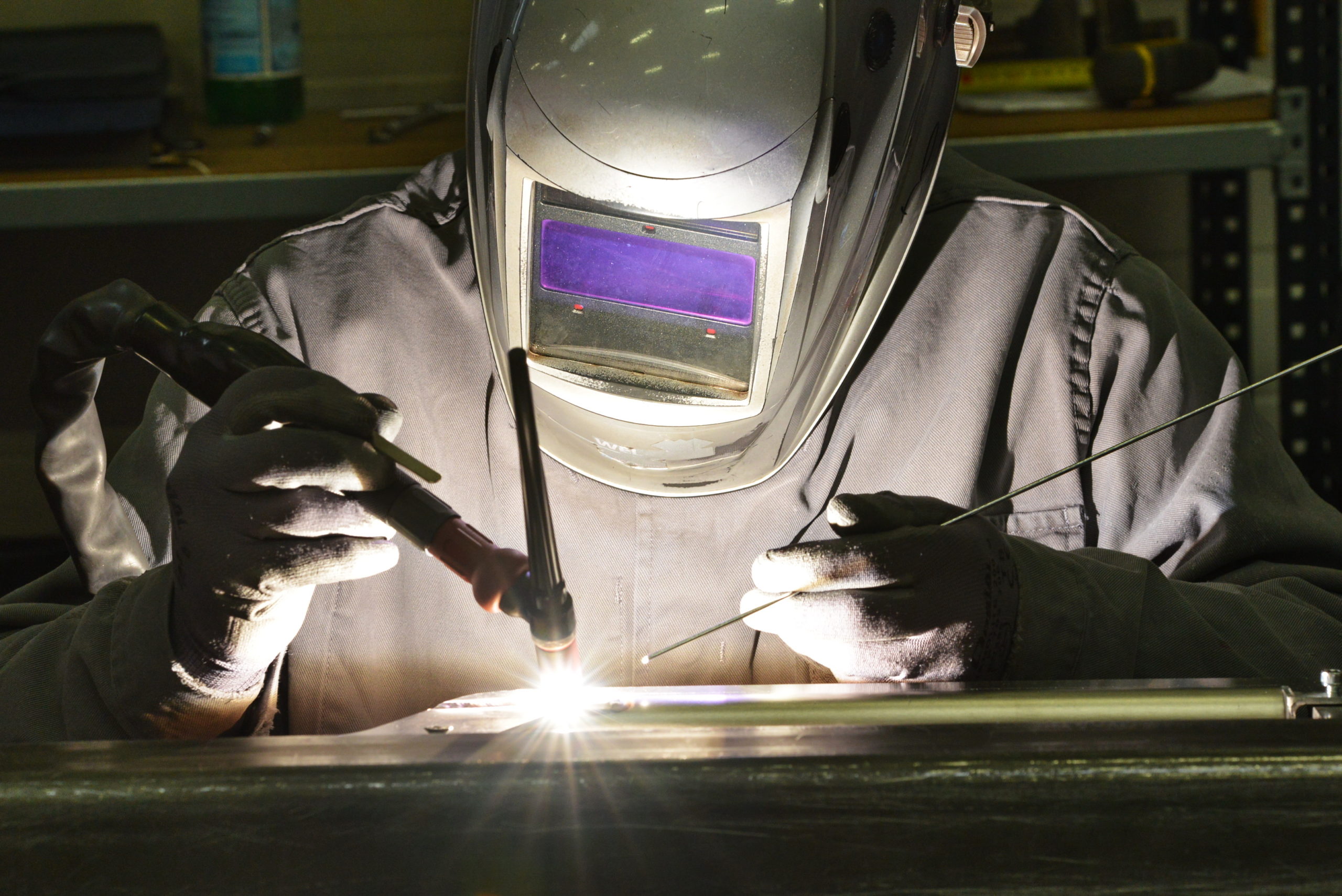
Review of the pros and cons of TIG welding
The cons:
The TIG welding process requires technical knowledge and know-how acquired through experience. Moreover, during the operation, you have to manage the different intensities as you go, a degree of finesse that has consequences and can sometimes seem difficult for a beginner. Training in TIG welding is therefore recommended and eliminates these drawbacks.
Compared with other processes, one can estimate that the TIG welding speed is lower in productivity and requires high energy consumption.
Pros
Its compatibility with working all metals and all thicknesses is no longer needs to be emphasised. It provides unparalleled versatility. Visually, TIG welds provide a highly appreciated aesthetic result. Its equipment is also increasingly compact and therefore allows access to difficult places.
Robotics increases the possibilities tenfold by offering orbital welding or even by optimising timing, input settings and TIG welding speed. In addition, TRA-C Industrie, thanks to its subsidiary STA, offers TIG welding training with highly qualified expert trainers (IWE, IWT, IWS, IWP, Meilleur Ouvriers de France).
TIG welding is as motivating as it is efficient. It widens the possibilities of the realisation of mechanical structures while achieving exact results. TRA-C Industrie, an expert in metalworking, provides welding subcontracting for the simplest to the most sophisticated assemblies. A partner of choice for creating mechanically welded structures, it also designs and manufactures tailor-made solutions for automatic welding machines and trains welders in best practices.
