Aluminum welding, the necessary expertise
Aluminum is the ideal ally when looking for lightness and robustness, which explains why it is found so much in aeronautic and automotive construction. It exhibits remarkable physical properties but delicate during assembly. With such specificities, can we weld aluminum? How can we weld aluminium with good mechanical strength? Here is an overview of aluminum welding.
The special characteristics of aluminum
Aluminium and its alloys have specific properties, which have earned them significant development.
- The density of aluminium is three times lower than that of steel, so it is light. As a result, in general, it meets the requirements of the aeronautics industry and the transport industry very well.
- It has excellent corrosion resistance, thanks to the alumina with which it is covered in contact with oxygen.
- Its electrical and thermal conductivity is very high.
- It is non-magnetic.
- It is robust: the mechanical resistance of pure aluminium is relatively low; however, the addition of other metals results in alloys with higher performance.
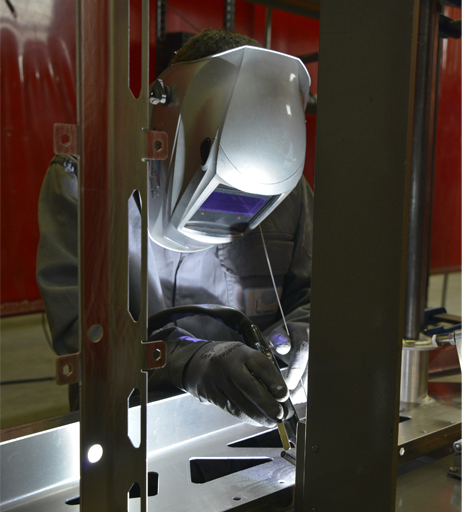

Can we weld aluminium and its alloys?
There are seven series of aluminium, which in principle allow aluminium welding. Each presents specific behaviours:
- 1000: pure aluminium, with excellent thermal and electrical conductivity;
- 2000: aluminium + copper to obtain a harder material;
- 3000: aluminium + manganese, very resistant to corrosion, with good weldability;
- 4000: aluminium + silicon, for forging;
- 5000: aluminium + magnesium, the most common in sheet metal, with excellent weldability, high resistance to corrosion and outstanding mechanical properties;
- 6000: aluminium + magnesium + silicon, often used for the construction of caravans;
- 7000: aluminium + magnesium + zinc, with good castability, easily machinable, good mechanical properties and corrosion-resistant.
So to the question “can we weld aluminium?”, our answer is “yes”. However, the 1000, 3000 and 5000 series offer the best weldability. On the other hand, the 2000, 4000 and 7000 grades may appear to be difficult to weld or require special precautions, with a tendency to crack and reduced mechanical qualities after welding. However, Friction Stir Welding makes it possible to weld the 2000 and 7000 series while optimising their mechanical characteristics.
Difficulties to overcome for aluminium welding
Aluminum welding is a technique in its own right, which is demanding and subject to precise constraints to achieve a high level of quality. TRA-C Industrie meets European certification EN 1090-1, which governs the manufacturing requirements necessary for high-performance aluminium welding for the production and assembly of its aluminium structures.
How can we weld aluminium?
Several processes can be used for welding aluminium or its alloys.
TIG welding of aluminium
It is one of the most readily adopted processes for producing aluminium welds. However, it should be noted that it must be alternating current in high frequency to strip the alumina film in low frequency to fuse the metal. This technique is appropriate for the assembly of elements of 1 to 4 mm, remembering that the addition of metal is useless up to 2 mm, but that beyond that, you will need a very high-power generator.
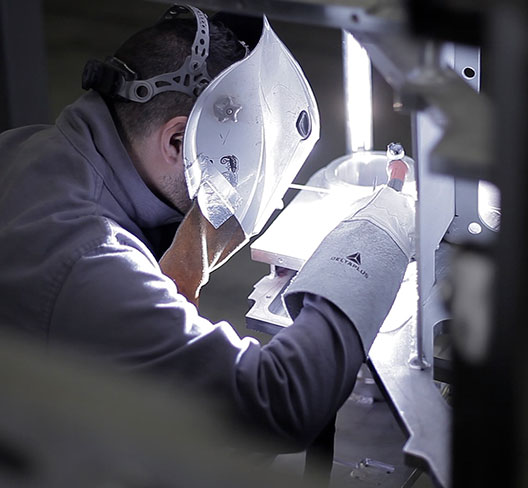

Aluminium welding with MIG
This process is very popular for thicknesses of more than 3 mm. Below that, it runs the risk of drilling and collapse of the aluminium weld bead. On the one hand, the MIG process requires accessories specific to aluminium and, on the other hand, careful degreasing to avoid the production of soot, and finally, a large diameter wire to limit the unwinding difficulties inherent to the softness of the wire. Argon is generally used or, depending on the alloy series and its thickness, an argon/helium mixture.
FSW: the best process for aluminium
The principle of the FSW (Friction Stir Welding) process is to make a rotating pin penetrate the parts to be assembled. Then, under the effect of friction and heating close to 500 degrees, their solid-state changes to a paste state, and the two elements mix.
This robotic welding has enabled decisive advances, particularly in successfully assembling aeronautical or automotive-type grades of aluminium that were not previously weldable. FSW connects aluminium and steel, which is very complex as their physical properties are too different.
The essential factor is understanding how to weld aluminium to achieve a high-quality result. With aluminium friction stir welding, distortions are almost zero, the bead perfectly sealed, the mechanical properties are high, often twice as high as conventional welding. This innovative technology is also economical, ecological and productive, with its welding speed up to 3 m/min. Currently, FSW, in which TRA-C Industrie is the European leader, is considered the best process for welding aluminium.
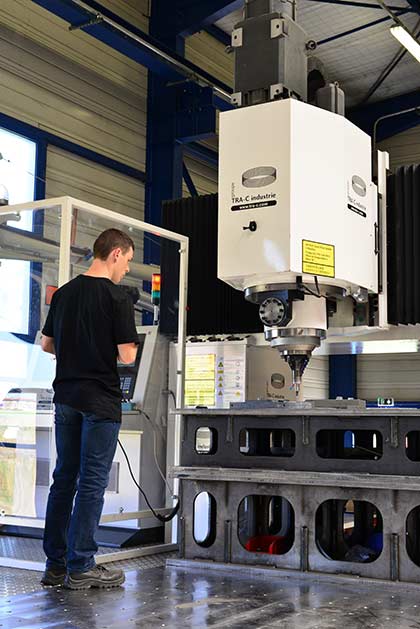
For many sectors of activity, the performance of aluminium structures determines the possibilities of developing markets or carrying out projects. It is, therefore, necessary to be able to rely on mastered technical expertise and optimal quality manufacturing.