Choosing The Right MIG Welding Gas
One of the most common and best ways to use a MIG welder is with solid wire and a cylinder of gas. It helps you to produce a slag-free weld and diminishes the needs to replace the electrode. There are many benefits of using a MIG welder such as increased productivity and a cleaner workspace, which is why it is an attractive method favoured by many.
However, to successfully use a MIG welder, you will firstly need to understand the role of this type of welding manufacturing machine and the different types of gas that you can use with it. Let’s discuss…
The Utility of MIG Welding Gas
Depending on your goals and your welding applications, you will need to determine what MIG welding gas you will use. There are a few things that you should consider like the cost of the gas and the finished weld properties. You should also consider the preparation and post-weld clean up, the base material, the weld transfer process and your productivity goals.
The purpose of the gas is to prevent exposure of the molten weld pool to oxygen, hydrogen and nitrogen contained in the air atmosphere. If these elements react with the weld pool it can create a variety of problems such as excessive spatter.
There are four common types of MIG welding gas. These are Carbon Dioxide (CO2), Argon, Oxygen and Helium. Let’s discuss each one in more detail.


Carbon Dioxide (CO2)
The most common out of all four gases has to be Carbon Dioxide (CO2). Instead of using an additional inert gas, CO2 can be used in its pure form. It is the only one of the four gases that can be used as it is. When it comes to price, CO2 is also the least expensive. This is ideal if your material costs are a priority which makes it an attractive choice for a lot of buyers.
One of the major benefits of CO2 is its ability to weld thick material. This is because the gas itself provides a very deep weld penetration. However, this can have its downfalls as it can produce more spatter when mixed with other gases.
Argon
Argon is an inert gas which is frequently used in MIG welding. It has many great benefits such as greater arc stability and reduced spatter. In comparison to CO2, Argon produces a narrower penetration profile. If you are looking to create fillet and butt welds, then this is ideal. You would need to use 100% Argon if you’re welding a non-ferrous metal such as aluminium or titanium.
You can combine Argon with CO2 to increase the weld quality and appearance. It is important to note that Argon is one of the more costly gases. However, combining it with CO2 can help you to reduce the overall costs of your project.
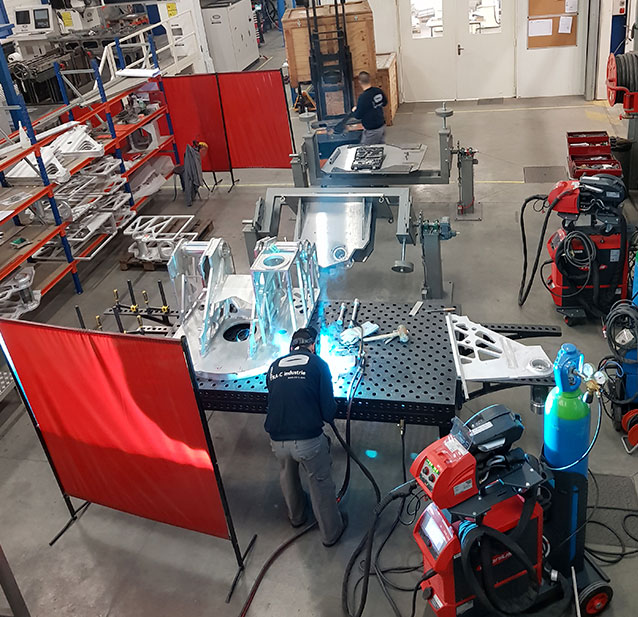

Oxygen
Oxygen is a particularly useful gas if you want to improve the weld quality and penetration. You cannot use this gas alone as it can cause corrosion. Typically, it is used with CO2 or Argon. It is recommended that you use Oxygen on mild carbon, low alloy and stainless steel. Because of its ability to corrode metal, it is advised that you stay away from using Oxygen with metals like magnesium and copper.
Helium
Similar to Argon, Helium is a Mig welding gas that is generally used with non-ferrous metals as well as stainless steel. Helium works well with these thicker materials as is produces a wide and deep penetration profile. When it comes to stainless steels, Helium is typically used in a tri-mix formula of Argon and CO2. This helps to reduce costs again as Helium can be one of the more expensive gases out there.
Typically, this gas is used in ratios between 25 – 75 percent Helium to 75 – 25 percent Argon. If you adjust these ratios, you can expect a change in the penetration, bead profile and travel speed. One of the attractive benefits of using Helium is its higher productivity rates. This is achieved because the Helium creates a hotter arc which provides fast travel speeds.
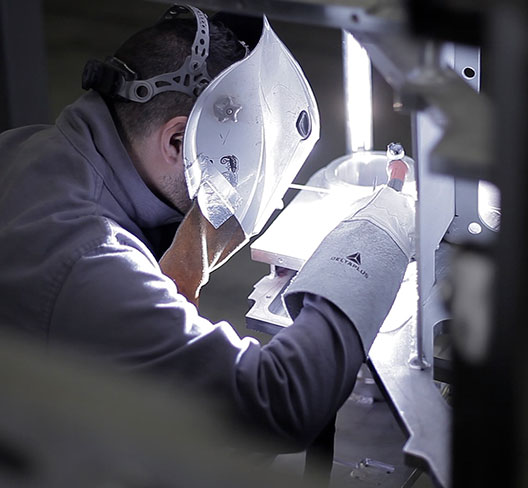
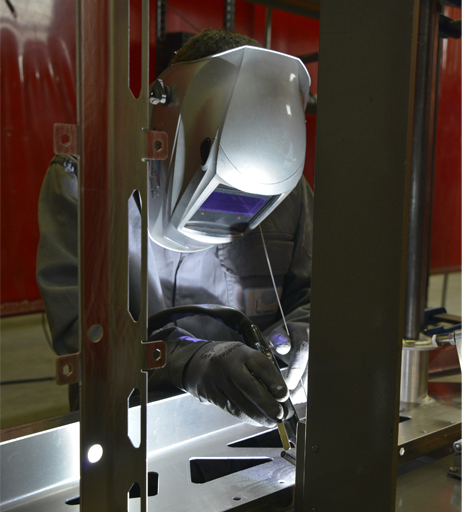
How To Pick the Right Option
In order to pick the right MIG welding gas for your specific application, you will need to conduct a thorough analysis of the type of welding that you are doing. It is important that you choose the right MIG gun consumables. Without the right equipment, the gas will struggle to get to the weld and all of your efforts to search for the right gas will be wasted.
The nozzle is a small but crucial part of MIG gun consumables. Too narrow and you risk an increase of spatter because it will become clogged. Ideally, you need to opt for a nozzle that is wide enough for adequate gas coverage. If you need advice on the quality of equipment, then TRA-C industrie can help. Our team of experts have years of experience in handling MIG welders and can steer you in the right direction when it comes to choosing your equipment.
Price point is also something that should be considered when choosing the right gas. If you need to keep your project costs low, then it can be wise to choose a gas like CO2. Although Argon is an inert gas that can increase the overall quality of your weld, you can expect to pay a lot more for it as it is a more difficult gas to extract. So, it is important to take that into consideration, so you don’t overspend on your project costs.
Why TRA-C industrie?
For years, our team of experts have helped and supported many clients in the design and implementation of specific projects. With experience and knowledge in welding, we can help to guide you in the right direction of which gas you should choose for MIG welding. We always advise that you consult with our team before making your final decision and we can assist you in achieving your project goals. For more information on how we can help, don’t hesitate to contact us via our website.