How to automate a production line?
The automation of a production line refers to the use of technology to perform tasks that were previously carried out by humans. The implementation of automation can lead to increased productivity, reduced labor costs, and improved quality control. However, it requires careful planning and implementation to ensure success. This guide will provide a step-by-step approach to the automation of a production line.

Step 1: Analyze the existing production line
Before automating a production line, it is important to understand the existing process. This includes the tasks performed, the equipment used, and the labor required. This analysis will help identify areas where automation can have the most impact.
Step 2: Identify the tasks suitable for automation
Not all tasks can be automated, and some may not be cost-effective to automate. The tasks that are suitable for automation include those that are repetitive, dangerous, or require precision. These tasks are often monotonous and can lead to human error. By automating these tasks, the risk of error is reduced, and productivity can be increased.
Step 3: Determine the level of automation required
Automation can be implemented at various levels, depending on the complexity of the process and the available budget. The four levels of automation include:
- Level 1: Basic Automation – involves the use of sensors, switches, and simple control systems to automate basic tasks such as on/off functions.
- Level 2: Machine Automation – involves the use of programmable logic controllers (PLCs) to control the operation of machines.
- Level 3: Supervisory Automation – involves the use of computer systems to control multiple machines and processes.
- Level 4: Enterprise Integration – involves the integration of automation systems with business systems such as inventory management and supply chain management.
The level of automation required will depend on the complexity of the production line and the budget available.
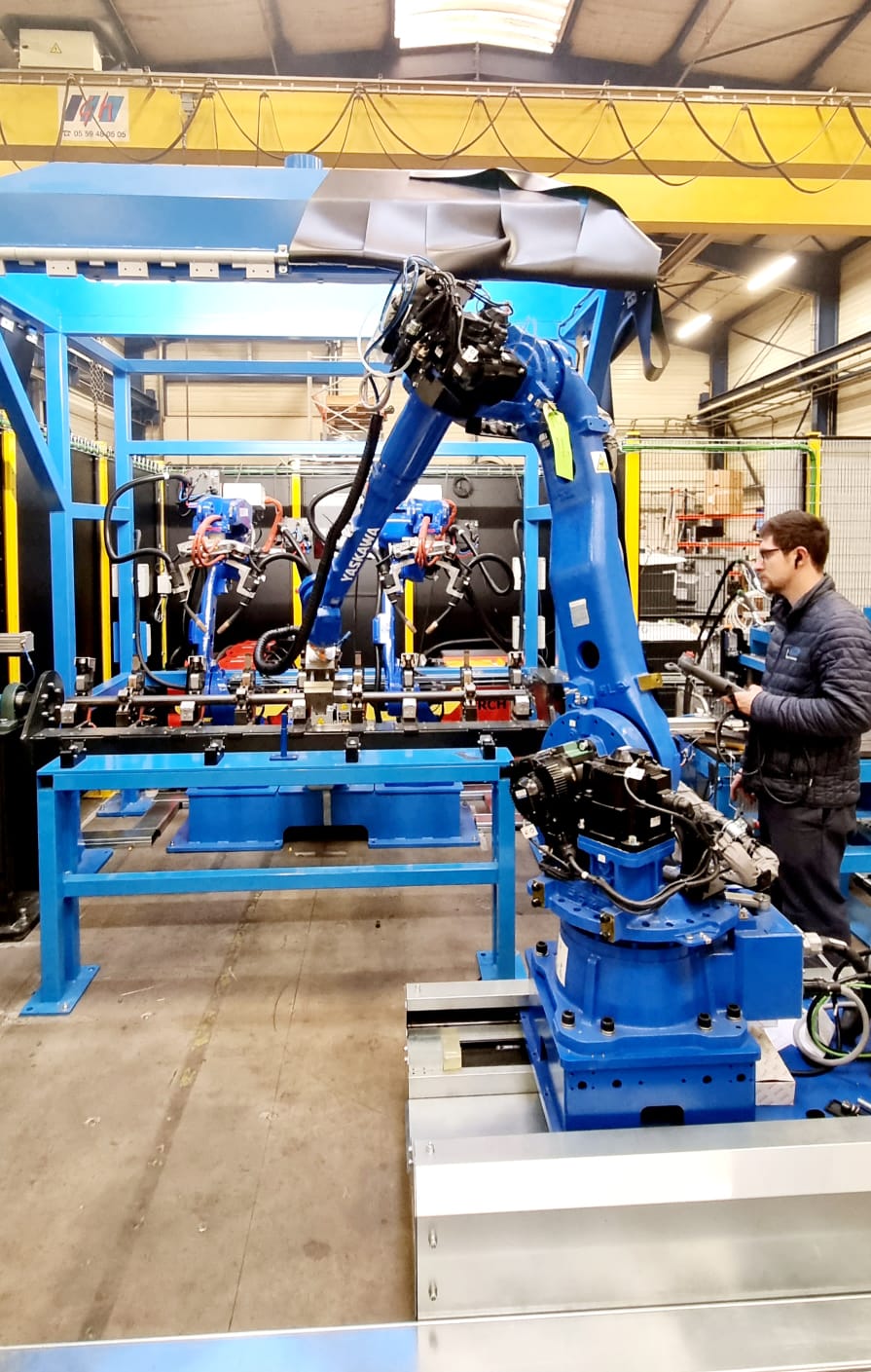
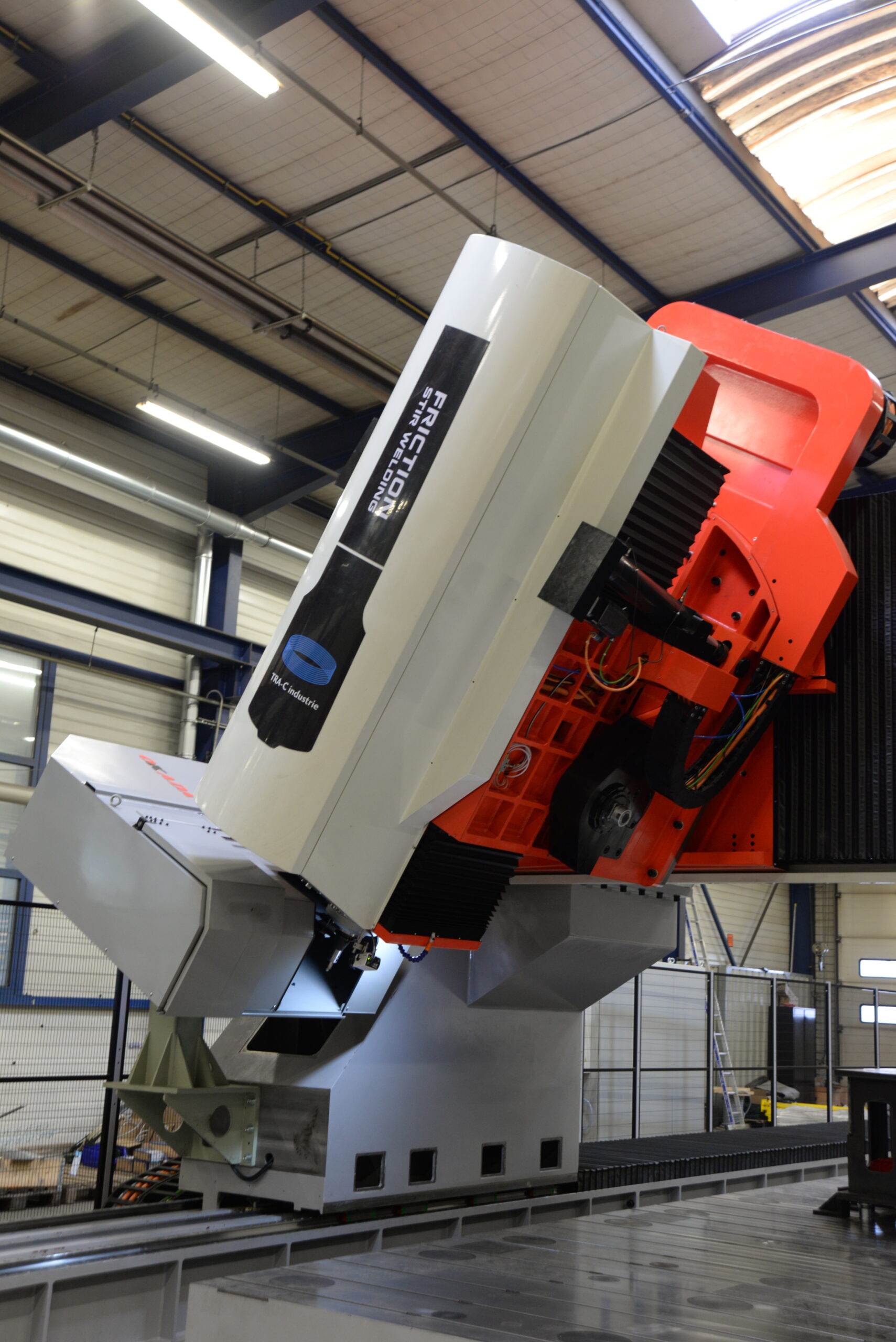
Step 4: Select the appropriate equipment
The selection of equipment is critical to the success of the automation project. The equipment should be reliable, easy to maintain, and compatible with the existing equipment. It is also important to select equipment that is scalable, to allow for future expansion.
Step 5: Develop a detailed automation plan
Once the equipment has been selected, it is important to develop a detailed plan for the automation project. This plan should include the following:
- A timeline for the project
- A budget for the project
- A list of tasks to be automated
- A list of equipment required
- A list of personnel required
- A risk assessment
The plan should be developed in consultation with all stakeholders, including production staff, management, and suppliers.
Step 6: Install and test the automation system
Once the plan has been developed, the automation system can be installed. This involves connecting the equipment, programming the PLCs, and testing the system. It is important to test the system thoroughly to ensure that it is operating as expected and to identify any issues that may arise.
Step 7: Train staff on the new system
The staff who will be operating the new automation system should be trained on how to use it. This training should include how to operate the equipment, how to troubleshoot problems, and how to maintain the system. It is important to provide ongoing training to ensure that staff are comfortable with the new system and can operate it effectively.

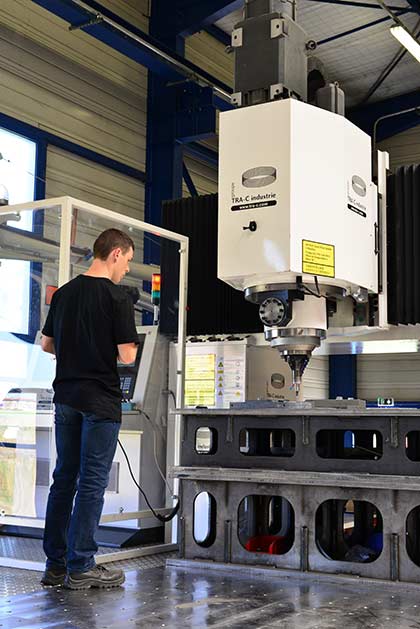
Step 8: Monitor and evaluate the system
Once the automation system is operational, it is important to monitor and evaluate its performance. This involves tracking productivity, identifying any issues that arise, and making adjustments to the system as required. Regular maintenance is also important to ensure that the system operates reliably.
Step 9: Continuously improve the system
Automation is not a one-time event, but rather a continuous process of improvement. It is important to continuously evaluate the system and identify areas for optimization and enhancement. This can be done by collecting and analyzing data, seeking feedback from users, and staying up-to-date with the latest technology and industry trends. By continually improving the system, you can ensure that it remains effective, efficient, and relevant to the needs of your organization and its stakeholders.
Automation has transformed the manufacturing industry by making it more efficient and cost-effective. Automation of a production line involves the use of machinery and technology to automate manufacturing processes, resulting in reduced labor costs, increased productivity, and improved product quality. In this guide, we will provide a comprehensive overview of the automation of a production line, including the benefits, challenges, and steps involved.
Benefits of Automating a Production Line
- Improved Efficiency and Productivity: Automation of a production line eliminates human errors and speeds up manufacturing processes, resulting in higher production rates and improved efficiency. Automated systems can run 24/7 without requiring breaks, which means that manufacturing facilities can increase their output significantly.
- Reduced Labor Costs: Labor is one of the biggest costs in manufacturing, and automating a production line can reduce these costs significantly. Machines can work faster and more accurately than humans, and they don’t require breaks, overtime, or sick days, which can save a lot of money for the company.
- Improved Quality Control: Automated systems can monitor the production process in real-time, which means that any defects or errors can be identified and corrected immediately. This results in better quality products and fewer defects, which can improve customer satisfaction and reduce the costs associated with product recalls.
- Increased Safety: Many manufacturing processes can be dangerous for humans, and automating these processes can improve safety in the workplace. Machines can perform tasks that are too dangerous or hazardous for humans, reducing the risk of accidents and injuries.
