Optimized friction stir welding
Friction stir welding or FSW has proven itself in the industrial world for about 20 years. All sectors are concerned by the benefits of this high value-added technology, whether in the aeronautics, automotive, nuclear, energy or pharmaceutical industries. High quality joints, speed of execution, lower assembly costs, environmental considerations, the arguments for friction stir welding are undisputed. To get the most out of it, it is important that the process is done perfectly. TRA-C Industrie gives you the key points to consider.
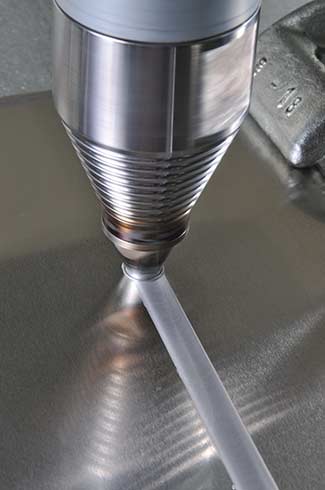
FSW technology in brief
Very popular for the assembly of aluminum parts as well as for the realization of parts with a high degree of requirement, the FSW process is a guarantee of quality and productivity. Why? Its very principle of welding without fusion explains its performance.
Unlike conventional methods, this technology does not cause a temperature rise and works without any material input. The optimized friction stir welding cell uses the friction of the elements to be joined thanks to a rotating pin. This transforms the original state of the material into paste. The metal parts to be joined mix at their junction, creating a flawless weld seam.
This technology is therefore economical in consumables. Ecological, it generates no smoke, no gas, no splashes and boosts productivity while reducing quality incidents.
By simply adjusting the settings to the configuration involved in the manufacturing process, friction stir welding is optimized and efficient.
Friction stir welding: what does it mean?
The FSW process is an advanced, high precision technology. It is therefore essential that it is always correctly implemented to obtain a good execution result. Furthermore, programming an optimized friction stir welding process requires an excellent knowledge of metals, an expertise acquired over time, as well as a careful attention to the destination of the final product.
Indeed, the type of parts to be assembled, but also the type of assembly, the nature of the alloys, their dimensions, their thickness, are as many criteria which influence the parameterization of the process. Hence the crucial importance of adjustments calculated beforehand, custom-made and with great precision.
TRA-C Industrie has a team fully dedicated to the research and development of FSW solutions. We analyze the applications of optimized friction stir welding and develop the determining variables specific to an environment. We are also able to carry out prototyping, as well as macroscopic and metallurgical analyses in our laboratory.

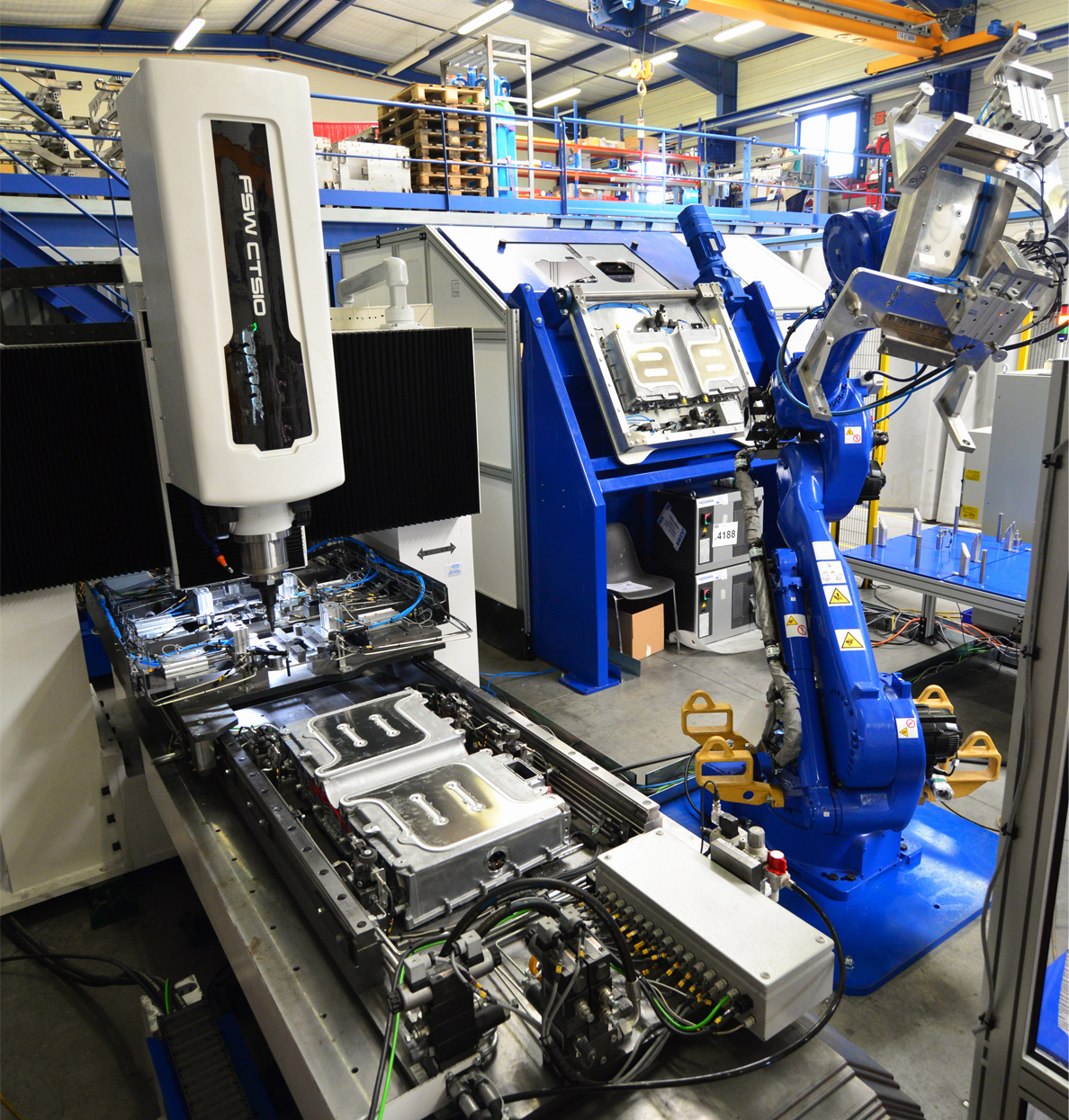
Optimized FSW in practice: why are these criteria important?
Each parameter of the optimized friction stir welding is the responsibility of a specialist and is subject to careful consideration:
- The threaded pinion and the shoulder: the first one penetrating the material, the second one stirring it, both contribute to its heating. The diameters and length are adapted according to the thickness of the part to be assembled and the type of assembly (butt to butt, square, T, or one part on the other by transparency)
- Control of the vertical force exerted by the pin: it must remain constant for impeccable repeatability and quality control, with the same level of adjustment, regardless of the possible relief of the parts. In addition, the penetration must be adequate so that it does not generate compactness defects or too small section.
- The calculation of the speeds: that of the rotation of the pin as well as the advancement of the tool on the seam. They depend as much on the nature of the alloy in question as on the size of the parts to be welded. Since they determine the heat reached by the metal during friction, they are decisive. Expertise is used to determine the best range between the two to achieve the ideal temperature and minimize energy costs.
TRA-C Industrie’s expertise provides the best combination of these characteristics, thus optimizing friction stir welding specifically for your production.