Manufacturing of robotic cells
Robotic cells, also known as robot cells or automation cells, are used in manufacturing to automate various processes, improve efficiency, create customized industrial robots and robotic solutions, and reduce costs. Robotic cells can be used in a wide range of industries, including automotive, aerospace, electronics, and healthcare. In this article, we will discuss the manufacturing process of robotic cells, including the design, construction, and programming.
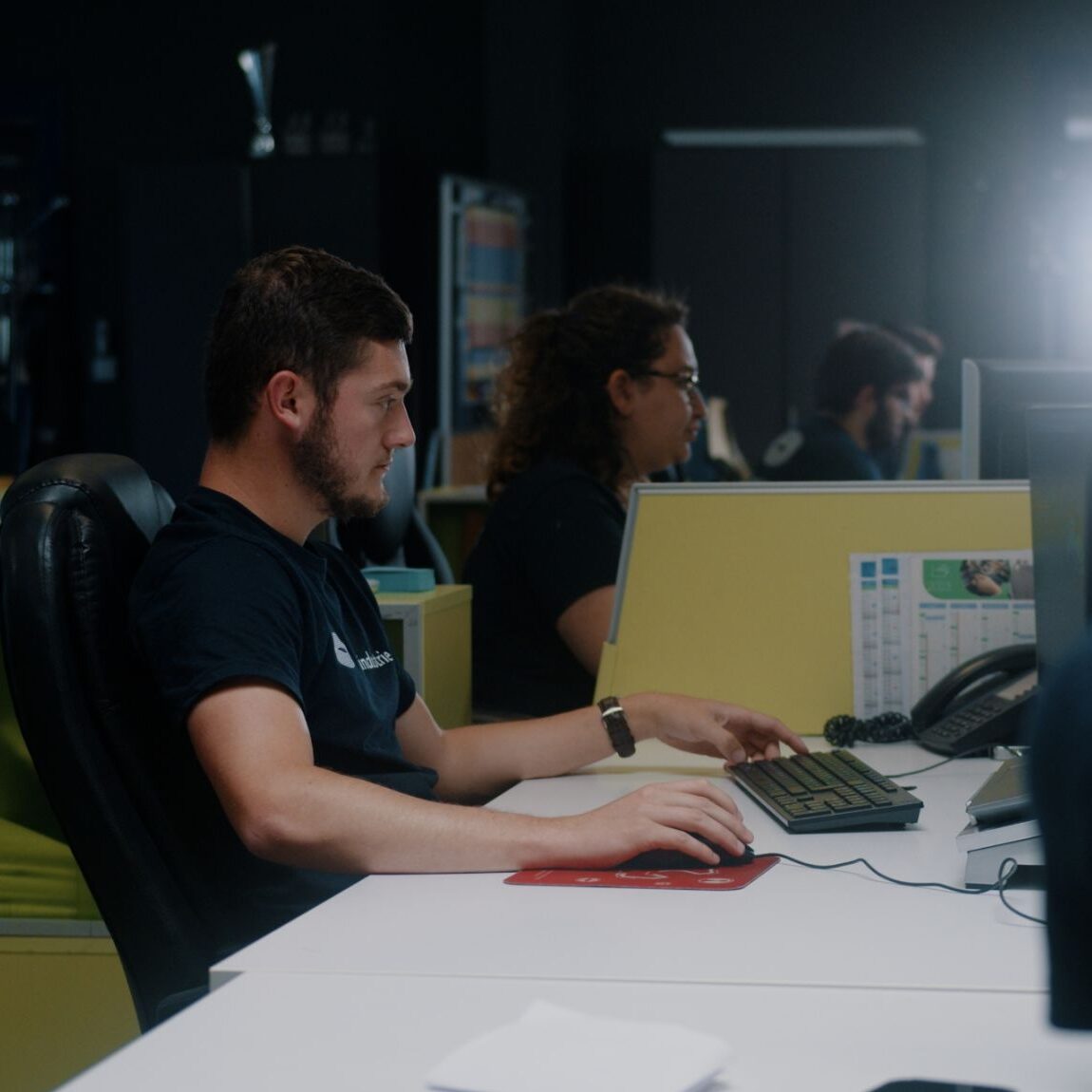
Design
The first step in manufacturing a robotic cell is designing the cell. The design process involves identifying the requirements of the application and selecting the appropriate robot, end-effector, and other components. The design must consider the size of the workpiece, the complexity of the process, and the desired throughput. Additionally, safety considerations must be taken into account, such as the need for fencing and safety sensors to protect operators from the robot.
The design process typically involves computer-aided design (CAD) software, which allows engineers to create a 3D model of the robotic cell. The CAD model is used to visualize the cell, identify any potential issues, and optimize the design before construction begins.
Construction
Once the design is complete, the next step is to construct the robotic cell. The construction process involves assembling the components of the cell, such as the robot, end-effector, and conveyor system. The construction process typically involves several stages, including mechanical assembly, electrical wiring, and programming.
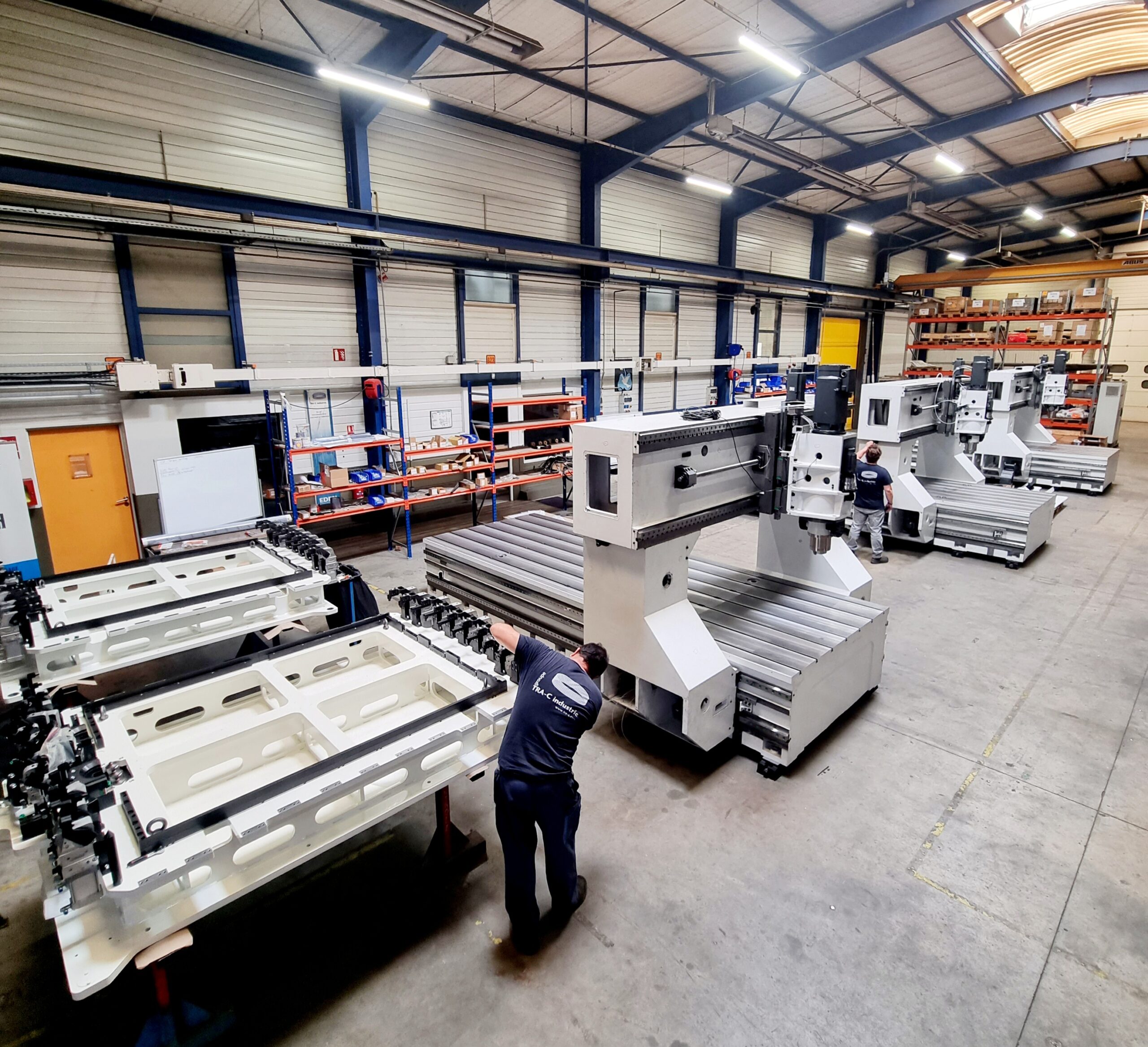
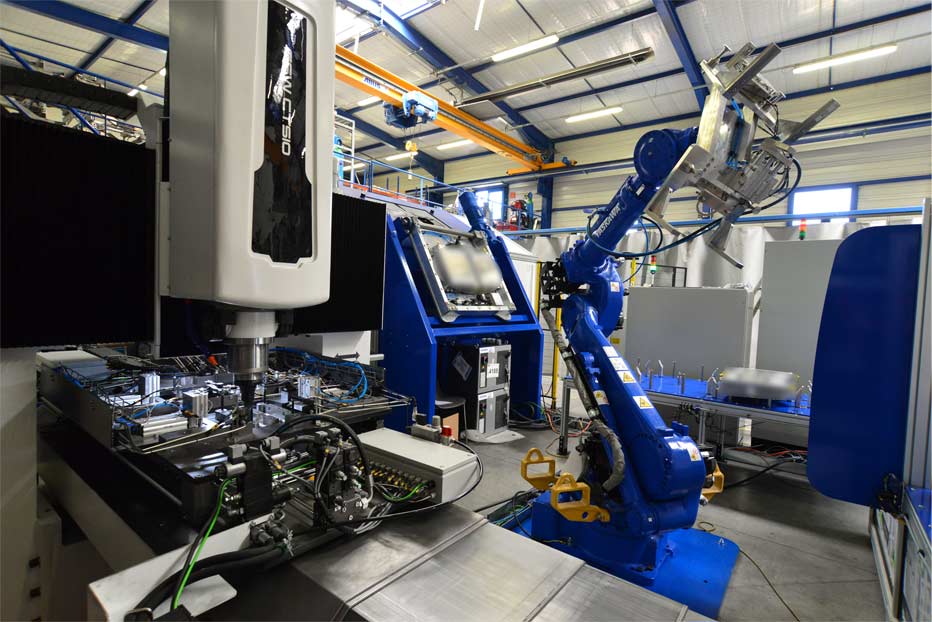
Mechanical Assembly
Mechanical assembly involves assembling the mechanical components of the robotic cell, including the frame, conveyor system, and robot arm. The frame provides the structure for the cell and supports the custom industrial robot and other components. The conveyor system is used to transport the workpiece through the cell, and the robot arm is used to perform the required tasks.
Electrical Wiring
After the mechanical assembly is complete, the next step is to wire the electrical components of the cell. This includes wiring the robot, end-effector, sensors, and other electrical components. The wiring must be carefully routed and organized to ensure that it is neat and easy to maintain.
Programming
Once the mechanical and electrical assembly is complete, the next step is to program the robotic cell. Programming involves creating the instructions that the robot will follow to perform the required tasks. The programming process typically involves several stages, including teaching, testing, and optimizing the program.
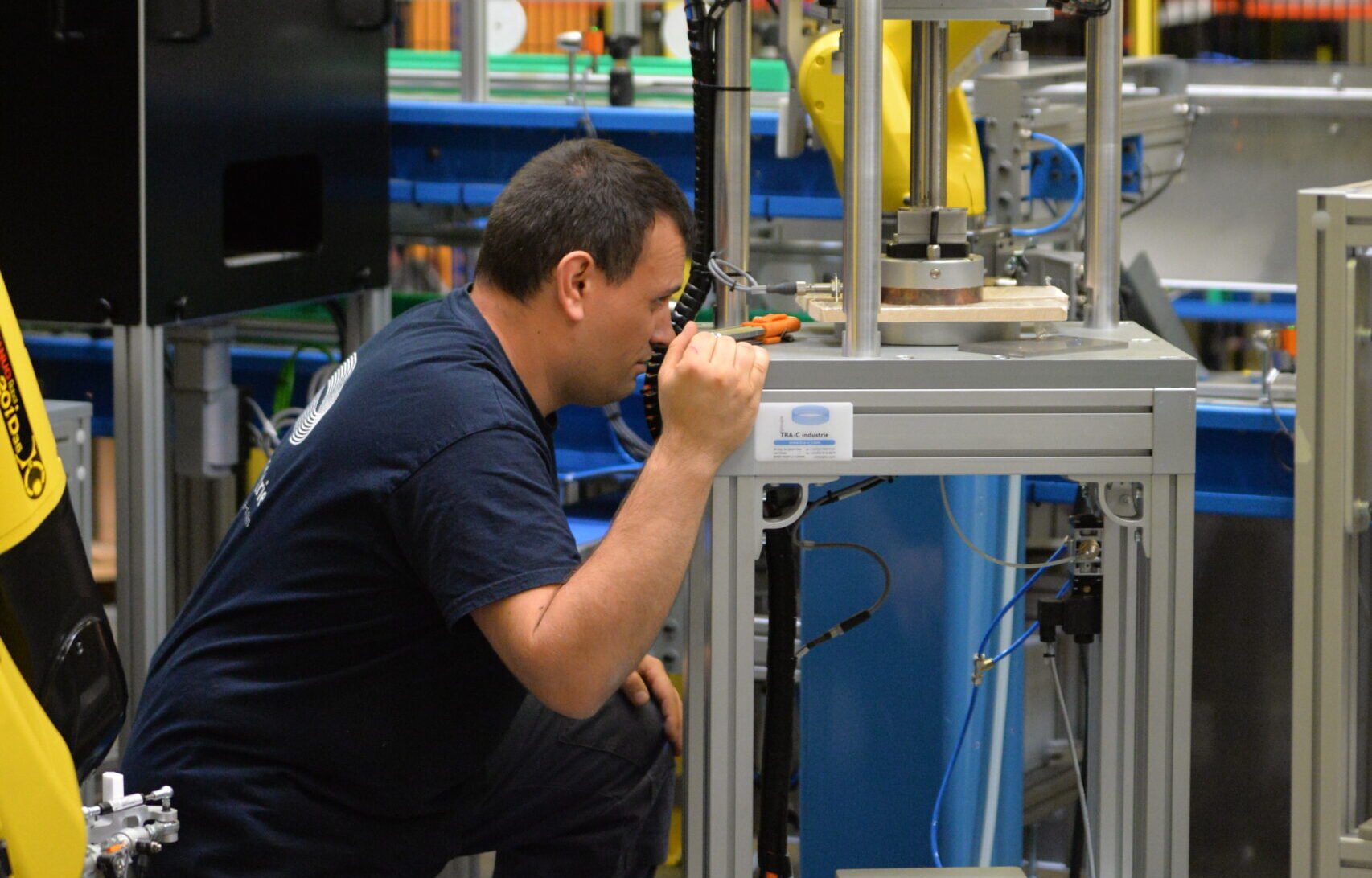
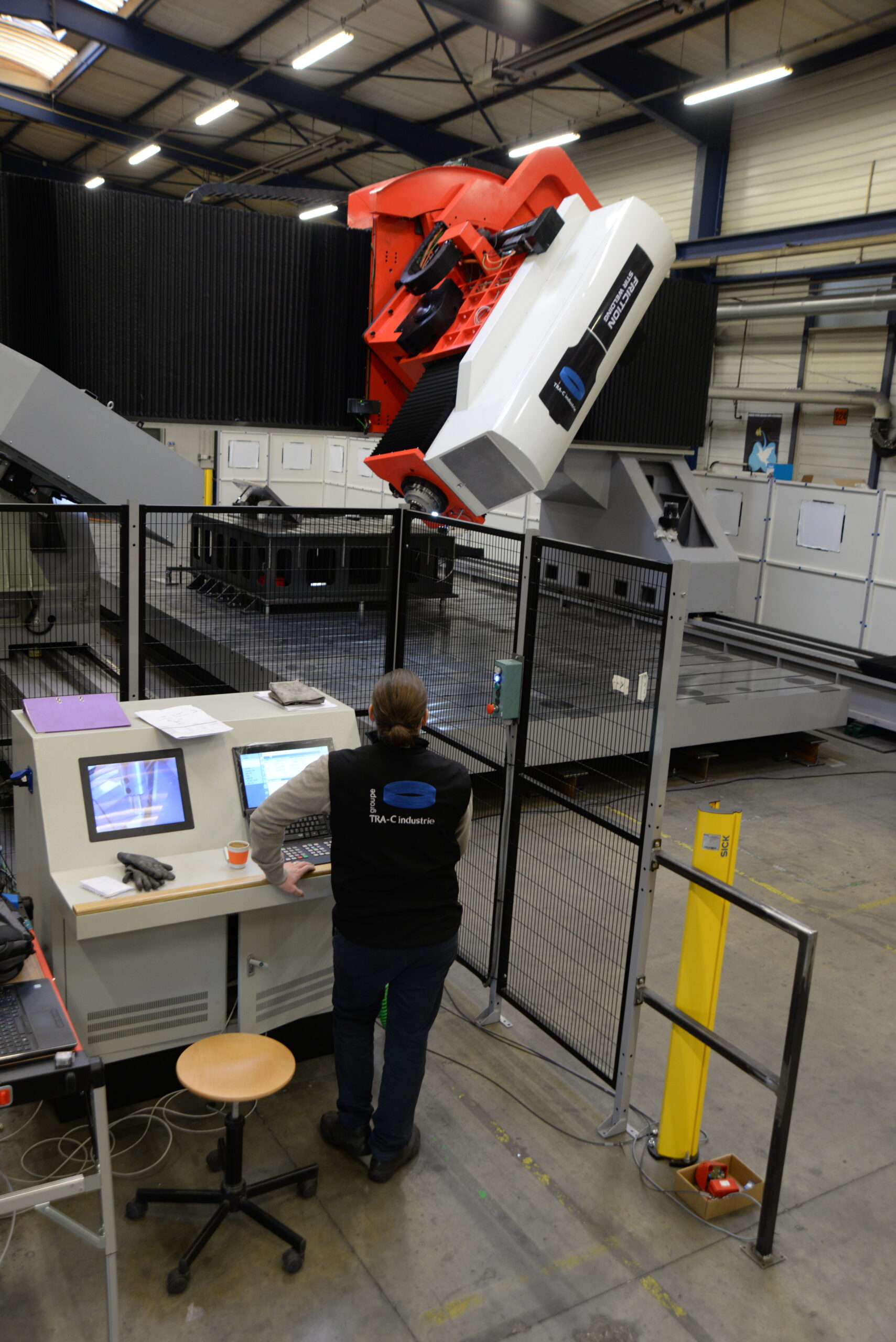
Testing
After the program is created, the next step is to test the robotic cell. This involves running the program and verifying that the robot performs the required tasks correctly. Testing is typically done in a controlled environment to ensure that the robot is safe and that the program is optimized.
Optimizing
Finally, once the program has been tested and verified, the next step is to optimize the program. This involves fine-tuning the program to improve efficiency and reduce cycle times. Optimization can involve adjusting the robot’s speed, acceleration, and deceleration, as well as optimizing the tool paths and programming logic.
Manufacturing robotic cells can be a complex and challenging process, but it can also yield numerous benefits for manufacturers. Some of the benefits of using robotic cells include increased productivity, improved quality control, and reduced labor costs.
Increased Productivity
Robotic cells can significantly increase productivity by automating repetitive or hazardous tasks that would otherwise require manual labor. Customized industrial robots and robotic solutions can work around the clock, allowing manufacturers to increase production rates and meet customer demand. Additionally, robotic cells can perform tasks more consistently and accurately than humans, resulting in fewer errors and rework.


Improved Quality Control
Robotic cells can also improve quality control by ensuring that tasks are performed consistently and accurately. Custom industrial robots can be programmed to perform tasks with a high level of precision, resulting in less variability in the manufacturing process. Additionally, robotic cells can be equipped with sensors and cameras to detect defects and deviations from the desired specifications.
In conclusion, manufacturing robotic cells involves a complex process that requires specialized expertise and resources. However, the benefits of using robotic cells can be significant, including increased productivity, improved quality control, and reduced labor costs. As technology continues to evolve, it is likely that the use of robotic cells in manufacturing will become more widespread, enabling manufacturers to further improve their efficiency and competitiveness.
