What are the stages in the design of a specialized machine?
In industrial production, manufacturing machines are used to produce the most diverse investment and consumer goods through a material processing process. These machines can perform a large number of operations, including drilling, milling, turning and welding, in order to create a final product with well-defined characteristics. Production machines are used in manual, semi-automatic or fully automatic form and are used in industry to improve the efficiency and accuracy of manufacturing processes.
Unlike a universal or multi-purpose machine, a special machine is used in a specific employment sector, within which it is characterized by a low unit cost. In particular, special machines are used to increase the efficiency of series and mass production.
The main difference between the two types of machines lies in their design purpose and functionality: while universal production machines can generally be used for a multitude of applications, special machines are optimized for a specific application and can provide better results thanks to their specialization.

Specialized machinery
A specialized machine is a type of production machine designed for a specific use or task. Unlike standard production machines which are suitable for a wide range of uses, special machines are designed and optimized for very specific tasks. These machines can automate complex processes, including carrying out checks, measurements and machining, in order to obtain a highly precise and repeatable result. Special machines are used in many different sectors, including the automotive and electronics industry, and can meet specific needs that general-purpose machines cannot provide.
Advantages of specialized machines
The use of specialized machinery has significant advantages for manufacturing companies in the most diverse sectors. This includes in particular:
- Efficiency: Special machines are optimized for a specific task and can perform it faster and more accurately than general production machines.
- Reduced costs: since they are specialized for a specific task, their industrial use results in increased productivity and reduced costs.
- Better quality: special machines are able to produce better quality products with greater precision.
- Flexibility: some special machines can be used for different tasks, which increases their flexibility.
- Greater safety: special machines are generally equipped with safety devices which considerably reduce the risk of accidents and errors.
- Time savings: the use of special machines can help reduce the workload and therefore save valuable production time.

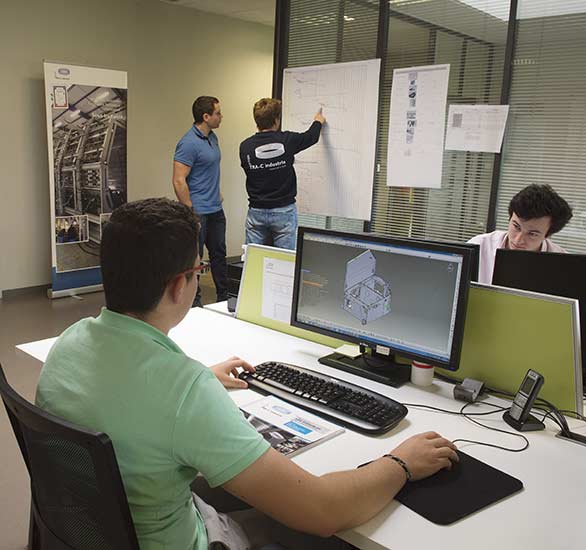
Construction of specialized machines
Designing a specialized machine is a complex process that requires careful planning, precise execution and detailed testing. We summarize below the main stages of the design of a special machine:
- Requirements analysis: To develop a suitable design, it is first necessary to determine the requirements that the special machine must meet. These include expected performance, size and weight of the machine.
- Concept development: different special machine concepts are then developed and compared in order to choose the best option. In order to optimize the design, existing technologies and their fields of application should also be taken into account.
- A detailed design: after choosing the best concept, the special machine is designed in detail, defining all the necessary components and systems. It is important to consider the specific performance, size and weight requirements of the machine determined previously.
- Prototyping: once the detailed design is complete, a prototype of the special machine can be built. This ensures that the finished product meets the overall requirements. Various tests also make it possible to check the performance and reliability of the machine.
- Manufacturing: once the prototype has been successfully tested, the manufacturing of the final special machine can begin. The meticulous workmanship of all components and systems ensures that the machine meets the needs.
- Commissioning: once manufacturing is complete, the special machine is installed and commissioned. On this occasion, all systems must be checked and retested to ensure that they are working properly.
Servicing and maintenance
To ensure long-term reliable operation, the special machine must be maintained and repaired regularly after commissioning. To avoid errors and breakdowns, the manufacturer’s recommendations should be followed. Maintenance can be carried out both by internal teams and by external service providers.
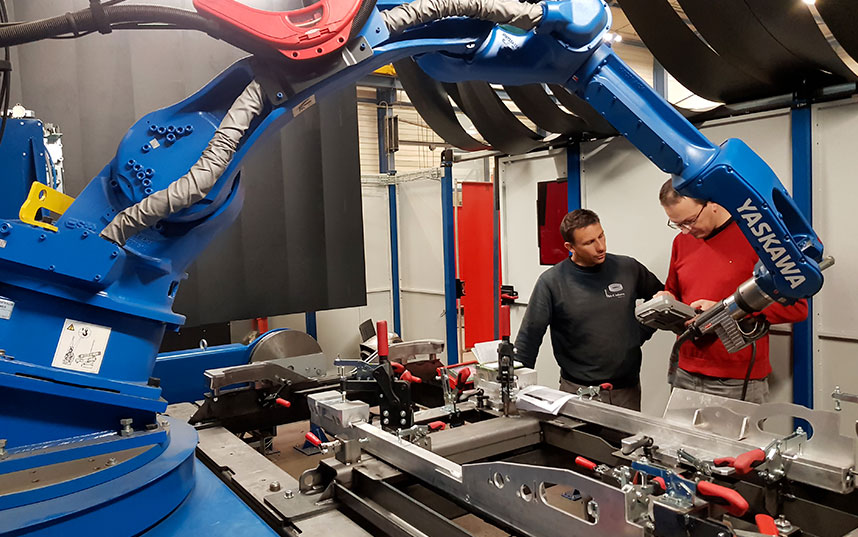
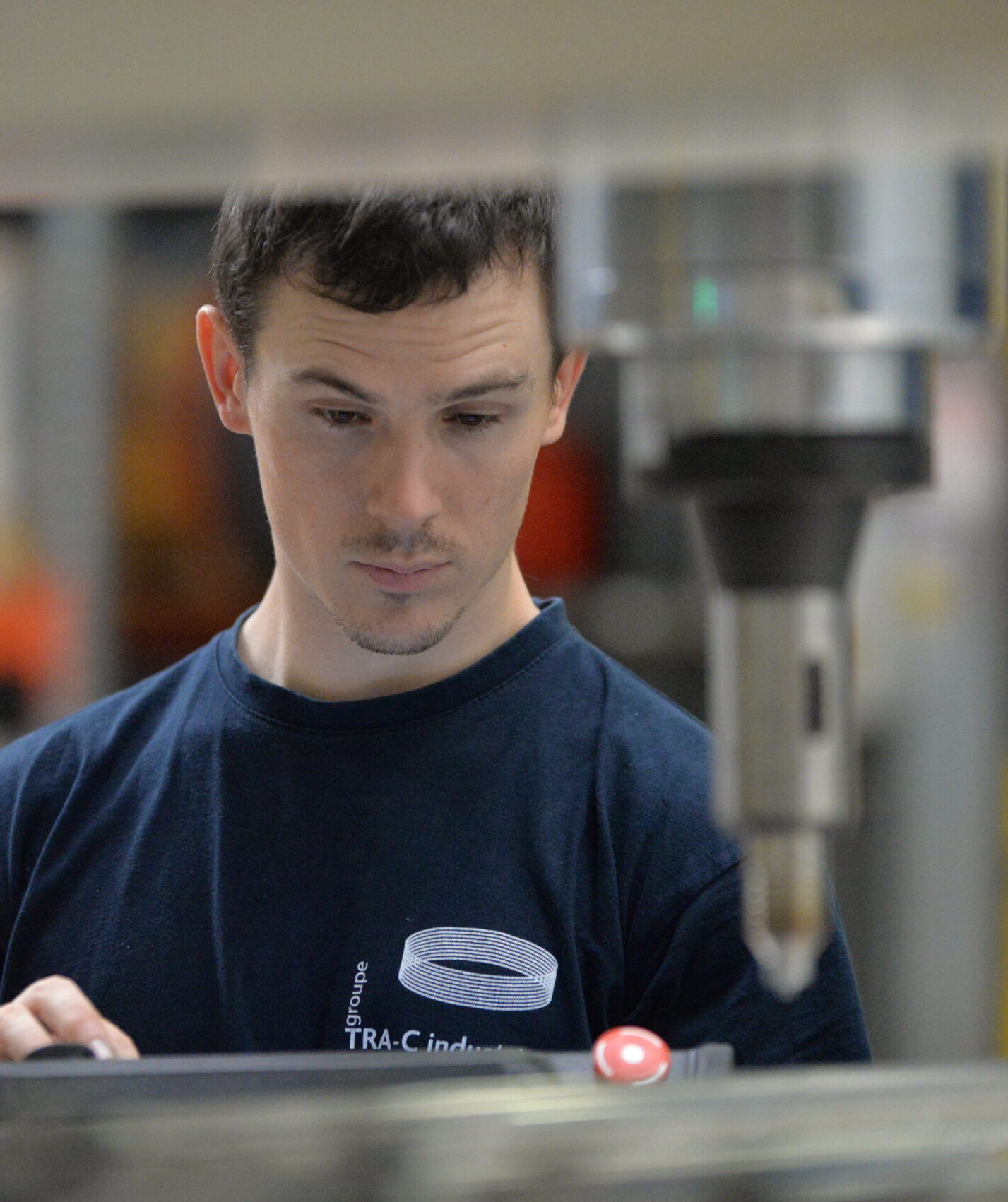
Industrial robots
By industrial robot, we mean an automated system that is used in production for a multitude of purposes. It is programmable and can perform different assembly, moving, material handling and manufacturing processes for components or entire products. In the automotive and electronics industry, industrial robots are used, for example, for welding, assembly and palletizing.
Industrial robots operate 24 hours a day, 7 days a week, particularly quickly and precisely, and can even perform dangerous and difficult tasks, which can increase productivity, reduce costs and improve quality goods produced.
While production machines and special machines are usually designed for a specific task, industrial robots offer greater flexibility and a greater capacity for automation: thanks to appropriate programming, they can be adapted to new tasks according to needs. To form a fully automated production line, industrial robots can also be integrated with other existing machines, plants and systems.
Choosing the right specialized machine
To ensure that a special machine meets internal business needs and optimizes processes efficiently, careful planning and construction are required. In order for the machine to retain its long-term performance and reliability after it is put into service, it must also be scheduled for regular servicing and maintenance.
A qualified supplier like TRA-C Industrie supports companies in the complex process of designing special machines and guarantees, through careful planning, precise execution and regular maintenance, that the machine meets the requirements in full and operates efficiently.
